What is the difference between 201 stainless steel and 304 stainless steel?
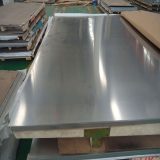
There are many soldering methods of aluminum alloys, and various methods have their different applications. In addition to conventional gwandering, resistance welding, gas welding method, other welding methods (such as plasma arc, electron beam welding, vacuum diffusion welding, etc.) can also be easily welded together.It should be selected according to the grade, welding of the aluminum alloy, the weldment of thickness, product structure, and the requirements of weldability.
Characteristics and Scope of Common Welding Methods for Aluminum Alloys
Welding method | Characteristic | Scope of application |
gas welding | Low heat power, large welding deformation, low productivity, easy to produce defects such as slag, cracks. | Thin plates for non-important occasions pair welding and rendering. |
Manual arc welding | Poor joint quality | Used in aluminum castings and general repairs. |
Tungsten argon arc welding | The weld metal is dense, the strength of the joint is high, and the plastic is good, and the quality joint can be obtained. | Applications wide, weldable plate thickness 1-20mm. |
Tungsten pulse argon arc welding | The welding process is stable, the heat input is accurately adjustable, the amount of solder is small, and the joint quality is high. | For thin plates, full position welding, assembly welding and high-strength aluminum alloys such as a forged aluminum, hard aluminum, and hard aluminum. |
Melted electrode argon arc welding | The arc power is large and the welding speed is fast. | For the welding of the thick member, the weldener thickness is 50 mm or less. |
Melting polar pulse argon arc welding | The welding is small, the anti-gas hole and the crack resistance are widely adjusted. | For thin plates or full position welding, it is often used in workpieces with a thickness of 2-12 mm. |
Plasma arc welding | The heat is concentrated, the welding speed is fast, the soldering deformation and small stress are more complicated. | Used to counter welding requires more argon arc welding. |
Vacuum electron beam welding | The melt deep heat is affected, the amount of welding deformation is small, and the linker has good mechanical properties. | Welding of soldering size. |
Laser welding | The welding is small and the productivity is high. | Welding for precision welding is required. |
The thermal power of oxy-acetylene gas welding flame is low, the heat is more dispersed, so the welding is large, the productivity is low. Preheating is preheated with gas welding with gas welding, the weld metal after welding is not only large, and the tissue is loose, but also defects such as alumina sand, pores and cracks. This approach is only used in a non-important aluminum finisher and welding of a casting of 0.5 to 10 ㎜.
This method is to weld by welding under argon, the heat is concentrated, the arc combustion is stable, the weld metal is dense, the strength and plastic welding joint is high, and the more wide application is obtained in the industry. Tungsten argon arc welding for aluminum alloys is a relatively complete welding method, but tungsten argon arc welding equipment is more complicated and should not operate in outdoor open-air conditions.
Automatic, semi-automatic melting argon arc welded arc power is large, the heat is concentrated, and the heat affected area is small, and the production efficiency is 2 to 3 times the manual tungsten argon arc welding. Pure aluminum and aluminum alloy plates having a thickness of 50 ㎜ less can be welded. For example, the aluminum plate of the welding thickness 30 ㎜ does not have to preheat, only welding is welded, and the two layers can be smooth and the surface of the surface can be smooth and the quality is excellent. Semi-automatic melting argon arc welding is suitable for positioning weld, intermittent short weld and structural shape irregular welding, which can be conveniently and flexibly welded with semi-automatic argon arc welding torch, but the semi-automatic welding wire diameter is fine. The pore sensitivity of the weld is large.
This method can significantly improve the stability of small current welding processes, which is convenient for controlling arc power and weld formation by adjusting various process parameters. The weldment is small, the heat affected zone is small, especially suitable for sheets such as sheets, full positional welding and other forged aluminum, hard aluminum, super hard aluminum, and the like for thermal sensitivity.
The average welding current can be used, the parameter adjustment range is large, the modifications of the weldment and the heat affected area are small, the productivity is high, the anti-gas hole and the crack resistance are good, suitable for all position welding of the thickness of 2 to 10 ㎜ aluminum alloy sheets.
Aluminum alloy sheets that can be used to weld thickness at 4 ㎜. For products with higher quality requirements, DC impact wave spot welding can be welded. When welding requires a more complex device, the welding current is large, the productivity is high, especially for large quantities of zero, components.
Stirring friction is a solid state connection technology that can be used for welding of various alloy plates. Compared with traditional gwolding methods, mixed friction welding without splash, no smoke, no need to add wire and protective gas, no air hole, crack. Compared to normal friction, it is not limited by the shaft parts, welded joints. This welding method also has a series of other advantages, such as the mechanical properties of the joint, energy saving, no pollution, and low preparation requirements. Due to the low melting point of aluminum and aluminum alloy, it is more suitable for stirring friction welding.
Aluminum welding material
When welding aluminum alloys such as gas welding, tungsten argon arc welding, a welding wire is required. Aluminum and aluminum alloy wire are divided into two major categories: homogeneous welding wire and heterogeneous wire. In order to obtain a good welded joint, it should be considered from the welding member, and the wire suitable for the base material is selected as the filler material.
Choosing the weld wire First, consider the requirements of welds, and consider the mechanical properties, corrosion resistance, structure of the structure, color and crack resistance. The filling metal having a melting temperature is lower than the base material can greatly reduce the tendencase tendency between the thermal affected zone. For the weld joint strength of the non-heat treatment alloy, according to the order of 1000 series, 4000 line, and 5000 lines.
The wire containing 3% of 5000 wires should be avoided in the structure of the temperature of 65 ° C, since these alloys are sensitive to stress corrosion cracks, stress corrosion cracks occur in the above temperature and corrosion environment. The welding wire is used as a filling metal with a welding wire having an alloy content than the base material, and it is generally prevented from the crack tendency of the weld metal.
At present, the welding wire commonly used by aluminum alloy is a standard grade wire with a substrate metal component. When lack of standard grade wires, the narrow strip can be cut from the base metal. The more general welding wire is HS311. This wire is well fluid, and the shrinkage rate is small in the time of solidification, and the specific crack resistance is specifically. In order to refine the seam grains, improve the crack resistance and mechanical properties of the weld, usually added a small amount of Ti, V, Zr, such as the metamorphism.
The problems that should be paid attention to using aluminum alloy welding wires:
Direct factors affecting the sensitivity of cracks are the matching of the base material and the wire. The melting temperature is lower than the weld metal of the base material, and the crack sensitivity of the weld metal and the heat affected zone can be reduced. For example, when the solder silicon content is 0.6% 6061 alloy, the same alloy is used as weld, and the crack is very sensitive.
However, with a silicon content of ER4043 wire, since its melting temperature is lower than 6061 alloy, there is a high plasticity during the cooling process, so the crack resistance is good. In addition, weld metal avoid combination of magnesium and copper because Al-Mg-Cu has high crack sensitivity.
Industrial pure aluminum has the low strength, 4000 series of aluminum alloy, and 5000 series aluminum alloy strength is the highest. Although the aluminum silicon wire has high crack resistance, the silicon-containing welding wire has a poor plasticity, so it is necessary to avoid the use of silicon-containing welding wire after the welding is required.
The selection of the filling metal is related to the geometry of the base material, and the corrosion resistance requirements of the joint and the appearance requirements of the weldment. For example, in order to make the container have good corrosion resistance or prevent the contamination of the stored product from which the welded container of hydrogen peroxide is required to be high purity aluminum alloy. In this case, the purity of the filled metal is at least equal to the base material.
Model (grade), specifications and use of aluminum and aluminum welding rods
model | Brand number | Welding core material | use |
E1100 | L109 | Pure aluminum | Welding pure aluminum plate, pure aluminum container. |
E4043 | L209 | aluminum Silicon alloy | Welding aluminum plate, aluminum silicon casting, general aluminum alloy, ductum aluminum (except aluminum magnesium alloy). |
E3003 | L309 | aluminum Manganese alloy | Welding aluminum manganese alloy, pure aluminum and other aluminum alloy. |
The inert gas welded aluminum alloy has argon and helium. The technical requirements of argon were AR> 99.9%, oxygen <0.005%, hydrogen <0.005%, water <0.02 mg / L, nitrogen <0.015%. Oxygen, nitrogen increases, and the cathode atomization is deteriorated. Oxygen> 0.3%, the tungsten burn is intensified, more than 0.1% make the weld surface without gloss or black.
When tungsten argon arc welding, the AC high-frequency welding is selected for pure argon, and the large thickness plate is applied; DC positive electrodeborne welding is selected from AR + HE or pure Ar.
When the melting crime welding, when the plate thickness <25 turns, purified AR is employed. When the plate thickness is 25 ~ 50, an Ar + HE mixture of 10% to 35% Ar + HE is used. When the plate thickness is 50 ~ 75, an Ar + HE mixed gas added to add 10% to 35% or 50% HE is preferably used. When the plate thickness> 75, 50% to 75% of the AR + HE mixed gas is recommended.