What is the difference between 201 stainless steel and 304 stainless steel?
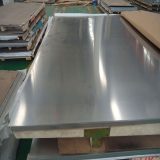
The thermal efficiency of oxy-acetylene gas welding is low, welded heat input is not concentrated, welding aluminum and aluminum alloy need to be melted, and after welding, the residue is required to remove residue, and the joint quality and performance are not high. Because the air welding equipment is simple, there is no need for power supply, the operation is convenient and flexible, and is often used to weld aluminum alloy members having high quality requirements, such as thin plates and small parts having thin thickness, and soldering aluminum alloy members and aluminum castings.
When the gas welding aluminum alloy, it is not advisable to use a lap joint and a T-shaped joint. This joint is difficult to clean the residual flux and weld slag flowing into the gap, and the docking joint should be used as much as possible. In order to ensure the welding of welding, it is welded and not collapsed and burned. It can be made of grooved pad, and the pad is generally made of stainless steel or pure copper, and the pad welding can obtain good back formation, improve welding productivity. .
When the aluminum is welded, in order to smooth the welding process, the weld quality is ensured, and the weld agent needs to be flmented to remove the oxide film and other impurities of aluminum surface.
The gas welding flux (also known as gas agent) is a flux of gas welding. The main function is to remove the oxide film generated in the aluminum surface during the gas welding, improve the wetting properties of the base material, and promote the dense weld tissue. The gas welding aluminum alloy must be felt, typically in the welded fuses directly on the grooved tank, or dip on the welding wire.
Aluminum alloy flux is a chloride salt of elements such as potassium, sodium, calcium, and lithium, which is pulverized after a sieve and a powder-like compound prepared in a proportion. For example, aluminum crystalline (Na3Alf6) can melt alumina at 1000 ° C, and such as potassium chloride, such as potassium chloride, such as potassium chloride, such as potassium chloride, can be converted to aluminum chloride. This flux has a low melting point and a good fluidity, and the fluidity of the molten metal can be improved, so that the weld is well formed.
Aluminum alloys have strong oxidation and intakeability. When gas welding, the aluminum is not oxidized, and a neutral flame or a weakly flavored flame (acetylene is both acetylene) is used to protect the aluminum fuser under the protection of the reducing atmosphere without oxidation. It is strictly forbidden to use the oxide, which will prevent aluminum in a strong oxidation of the oxidation, hinder the welding process; and the acetylene, free hydrogen may dissolve into the molten tank, which causes the slit to generate a pore, so that the weld is loose.
In order to prevent the weld from generating dimensions and relative positions in welding, it is necessary to pin welding before welding. Since the aluminum has a large line expansion coefficient, the heat conductivity is fast, the air welding is large, and therefore, the positioning weld is subject to the steel parts.
The filled welding wire of the positioning welding is the same as the product welding, and the gas is applied to the weld gap before the positioning welding. The flame power of the positioning weld is slightly larger than the gas.
When welding steel materials, the temperature of the heated can be determined from the color of the steel. But when soldering aluminum, there is no convenient condition. Because the aluminum alloy has no significant change in color from room temperature to melting, it is difficult to control welding temperature. However, according to the following phenomenon, the welder is grasped:
1) When the heated workpiece is turned from a white white, the surface oxide film wrinkles, the metal has fluctuations in the heating, indicating that the melting temperature is noted, can be soldered;
2) When the tip of the weld wire is used and heated, the wire and the base material can be fused, i.e., reach the melting temperature, can be soldered;
3) When the rib of the base material has fallen phenomenon, the base material reaches the melting temperature and can be soldered.
The air welding sheet can be used for the left welding method. This solder method is located prior to welding flames, which is partially directed to the uncoated cold metal and heat loss, which is conducive to preventing the molten tank overheating, and the thermal influence zone metal grain grows up and burned. The thickness of the base material is greater than 5 ㎜, the right welding method can be used. This method is welded behind the torch, the flame points from the weld, the heat loss is small, the melted is deep, and the heating efficiency is high.
When the thickness of the gas welding is less than 3 ㎜, the torch is incorporated from 20 to 40 °; when the gas welding thick member is 40 to 80 °, the welding wire and the torch angle are 80 to 100 °. Aluminum alloy gas welding should be welded once, without stacking the second layer, because the second layer can cause weld clamping.
The residual flux and slag on the surface of the gas weld weld to the corrosion of the aluminum joint are one of the reasons why the aluminum joint is damaged in the date of use. Within 1 to 6 hours of gas welding, the residual flux should be cleaned off to prevent the corrosion of the solder. The cleaning process after the welding is as follows.
1) After welding, the weldment is immersed in a hot water tank of 40 to 50 ° C, preferably with flowing hot water, weld the flush, and the slag, where the solder is removed, and the slag is removed.
2) Immerse the solder into the nitric acid solution. When the room temperature was 25 °, the solution concentration was 15% to 25%, and the immersion time was 10 to 15 min. When the room temperature was 10 ~ 15 ° C, the solution concentration was 20% to 25%, and the immersion time was 15 min.
3) Place the solder in the groove of flowing hot water (temperature of 40 to 50 ° C) for 5 to 10 min.
4) Rinse the solder for 5 min with cold water.
5) Dry the solder naturally, or dried in a dry box or blows with hot air.
Also known as the tungsten inert gas protection arc welding, is a large amount of heat generated by forming an arc between the tungsten and the workpiece, and the outer filling welding is obtained. Welding joint. Arc-arc welding aluminum is the characteristics of its "cathode atomization", and the oxide film is removed. The tungsten and seam regions are shielded from the inert gas discharged in the nozzle to prevent the weld zone and the surrounding air.
The TIG welding process is most suitable for thin plates having a thickness of less than 3 ㎜, and the workpiece deformation is significantly less than the gas welding and arc welding. The AC TIG welded pod has a clean-up effect of the oxide film, and can avoid the weld residual flux, the corrosion of the slag to the joint without a flux. The joint form can be unrestricted, the weld is well formed, and the surface is bright.
The iron gas flow improving the joint to the weld area, improve the tissue and performance of the joint, suitable for full position welding. Due to the need for the flux, the pre-welding requirements are strict than other welding methods.
The preferred process method for welding aluminum alloy is to communicate TIG welding and AC pulse TIG welding, followed by DC reverse TIG welding. Typically, the optimal cooperation can be achieved when using the AC welding aluminum alloy, and most of the aluminum alloy TIG welding uses AC power supply.
When DC is directly connected (electrode liability), heat is generated on the surface of the workpiece, forming a deep melt, and a larger welding current can be used for a certain size of the electrode. Even if the thick section does not need to be preheated, and the base material has almost no deformation. Although the DC reverse (electrode connection positive electrode) TIG welding method is used to weld aluminum, this method is in a shallow and arc when the tube is welded or soldered by a thin-walled heat exchanger. Easy to control, the arc has a good purification effect.
The melting point of tungsten is 3410 ° C, which is a metal having a maximum melting point. Tungsten has a strong electron emission capability at high temperatures, and after the tungsten rare earth element is added to the oxide of the tungsten rare earth element, the oxide, and the electron-producing power are significantly reduced, and the current carrier capacity is significantly improved. When the aluminum alloy TIG welding, the tungsten is mainly transmitted as the electrode to the conductive current, the ignition arc and the normal combustion of the arc. Commonly used tungsten material is pure tungsten, tungsten and tungsten tungsten or the like.
In order to obtain excellent weld forming and welding quality, the welding process parameters should be reasonably selected according to the technical requirements of the solder. The main process parameters of aluminum alloy manual TIG weld have a current type, polarity and current size, protective gas flow, tungsten polar length, and nozzle to the distance of the workpiece. The process parameters of the automatic TIG solder also include arc voltages (arc lengths), welding speed, and wire speed.
The process parameters are based on the welded materials and thickness, first determine the tungsten diameter and shape, wire diameter, protective gas and flow, nozzle pore, welding current, arc voltage, and welding speed, and adjust the relevant parameters according to the actual welding effect, until it is used Requirements.
The selection points of the aluminum alloy TIG welder parameters are as follows.
1) Nozzle aperture and protective gas flow
The nozzle pore diameter of the aluminum alloy TIG is 5 to 22 ㎜; the gas flow rate is generally 5 to 15 l / min.
2) Tungsten protubeth length and nozzle to workpiece distance
Tungsten is protruding: generally 5 ~ 6 ㎜ in the docking weld, and the angular weld is generally 7 to 8 ㎜. The distance from the nozzle to the workpiece is generally about 10 ㎜.
3) The welding current is related to the welding voltage from the thickness, joint form, welding position, and welder technology.
When manual TIG welding, an AC power supply is used, and when the welding thickness is less than 6 ㎜ aluminum alloy, the maximum welding current can be determined according to the electrode diameter D according to the formula I = (60 ~ 65) D. The arc voltage is mainly determined by the arc length, usually approximates that the arc length is approximately equal to the tungsten diameter.
4) Welding speed
When the aluminum alloy TIG welding, in order to reduce the deformation, a faster welding speed should be used. Manual TIG welding is typically welded according to the size of the molten pool, the fusion of the molten pool shape and both sides are adjusted at any time. The general welding speed is 8 ~ 12m / h; the automatic TIG welding, after the process parameter setting, during the welding process The welding speed is generally constant.
5) Welding wire diameter
It is generally determined by the thickness and welding current, and the wire diameter is proportional to both.
1) Causes of pores
The purity of argon or water is low in argon pipelines, air leaks, etc ; the welding wire or the parent material grooves are not cleaned or cleaned, and it is contaminated by dirt, moisture, etc; the welding current and the welding are too large or too Small; the fusion pool is poor, the arc is unstable, the arc is too long, and the tungsten is too long.
Preventive measures
To ensure argon pipeline, choose to carefully clean wire, welding, and timely welding, and prevent re-pollution. Update the gas pipeline, select the appropriate gas flow, adjust the length of the tungsten to extend the length; correctly select the welding process parameters. If necessary, a preheating process can be taken, and the soldering site is welded to prevent wind flow from the site.
2) Crack generation cause
The wire alloy component is not properly selected; when the magnesium content in the weld is less than 3%, or the silicon impurity content is exceeded, the crack tendency is increased; when the melting temperature of the wire is high, the heat affected zone is liquefied; structural design Unreasonable, the weld is too high or the temperature of the heat is too high, resulting in an excessive stress of the joint; the high turbid residence is long, the organizational overheating; the arc is not filled, there is an arc crack.
Preventive measures
The composition of the selected wire is to match the base material; add the arc assembly or by the current attenuation device to fill in the arc; correctly design the welding structure, reasonably arrange the weld, so that the weld is as possible to avoid the stress concentration, select the appropriate welding order Reduce the welding current or increase the welding speed.
3) Reasons for non-welding
The welding speed is too fast, the arc length is too large, the welding gap, the groove angle, the welding current is too small, the bluntness is too large; the burr of the edge of the workpiece, there is no net in the bottom of the dirt welding; torch and wire The inclination is incorrect.
Preventive measures
Correctly select gap, blunt sides, groove angles and welding process parameters; strengthen the cleaning of oxide films, flux, slag and oil; improve operational skills.
4) Weld joint tungsten generation cause
The contact arc is caused; the end shape of the tungsten is unreasonable to the welding current, so that the tip is disengaged; the filament is hit to the tungsten pointer and the misused gas.
Preventive measures
High-frequency high pressure pulse arc; according to the selected current, a reasonable tungsten tip shape is used; reduce the welding current, increase the tungsten diameter, shorten the length of the tungsten, update the inert gas; improve the operation skills, do not make the filament Contact with tungsten or the like.
5) Causes of the bite
The welding current is too large, the arc voltage is too high, the torch is not uniform, the filament is too small, the welding speed is too fast.
Preventive measures
Reduce the welding current from the arc voltage, keep the torch swing uniform, increase the transmission speed or reduce the welding speed.
The usual aluminum alloy castings can be soldered by argon arc welding processes, and the welding effect is better in exchange of TIG welding.
When the soldering process is used to reduce the casting defect rendering, in addition to the general practices mentioned above, such as the pre-welder, the wire and workpiece are welded, and the reasonable welding wire material is selected, and the short arc and small angle wire join method for welding and other points. In addition, there are many successful experiences for different defect types in practice, such as using small current welding;
The wire alloy ingredients when the soldering wire is selected higher than that in order to supplement the burning mixing in the solder process, so that the weld ingredient is consistent with the base material; the camped metal is suppressed before the castings with crack defects When welding should first be heated to weld the welded portion, the left welding method is used to facilitate the molten of the weld. After the welding is melted, the filament is fill it to form a sufficiently wetted molten pool;
When the defect size is large, in order to improve the soldering efficiency, it can be applied to the surface of the welding position, and the active agent can cause welding arc shrinkage or in the conventional TIG welding. The metal flow generated in the molten pool changes, so that the weld is deeply increased, and when the aluminum alloy exchange TIG welding is to apply a layer of SiO2 active in the weld surface to change the weld depth, reduce the preheating procedure and reduce welding. Difficulty.