What is the difference between 201 stainless steel and 304 stainless steel?
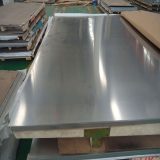
Aluminum alloy is very wide in our lives, mainly the weight, high hardness, and is widely used by people, but the welding of aluminum alloy is a high strength technology.
1)Aluminum is extremely easy to oxidize in air and welding, and the resulting alumina (Al2O3) has high melting point, very stable, and is not easy to remove. Hold the melting and fusion of the base material, the specific gravity of the oxide film is large, and it is not easy to surface, which is easy to generate lack of slag, unfelt, un welded. The surface oxide film of the aluminum and the large amount of moisture adsorbed, and the weld is easily produced. Chemical or mechanical methods should be carried out by chemical or mechanical methods before welding, and its surface oxide film is removed. Strengthen protection in the welding process to prevent oxidation. When tungsten isas, an AC power source is selected, and the oxide film is removed by "cathode cleaning". When gas welding, the flux of the oxide film is removed. When the thick plate is welded, the welding heat can be increased, for example, the amount of a helium arc is high, using helium gas or argon-helium mixed gas, or uses a large-specific molten atrial gas protection welding, in direct current, no "cathode" Clean up.
2)the thermal conductivity and more heat capacity of aluminum and aluminum alloy are more than twice the carbon steel and low alloy steel. The thermal conductivity of aluminum is more than ten times the austenitic stainless steel. During the welding, a large amount of heat can be quickly transmitted to the inside of the base metal, and therefore, when welding aluminum and aluminum alloy, the energy is consumed in the molten metal molten pool, and more heat is unnecessary to consume other parts of the metal, this The consumption of useless energy is more remarkable than steel welding. In order to obtain high quality welded joints, it should be used to use energy concentration and high power, and preheat can also be used.
3)The linear expansion coefficient of aluminum and aluminum alloy is about twice the carbon steel and low alloy steel. The volume shrinkage rate in aluminum is large, and the deformation of the weldment is large, so it is necessary to take measures to prevent welding deformation. When the aluminum welding is solidified, it is easy to produce a shrinkage, a pure, thermal crack and a higher internal stress. The production of adjustment welding wire components and welding processes can be used to prevent heat cracking. In the case of corrosion resistance, an aluminum alloy other than aluminum-magnesium alloy can be welded. When the silicon alloy is 0.5%, the thermal crack is large, as the silicon content increases, the alloy crystal temperature range is small, the fluidity is significantly improved, the shrinkage is lowered, and the thermal crack tendency is also reduced accordingly. Depending on the production experience, when a silicon is oricon-containing, no heat cracks can be produced, thereby using Salsi strips (silicon content 4.5% - 6%) Welding will have better crack resistance.
4)aluminum pairs of light, hot reflection ability, solid, liquid turning state, no significant color change, and it is difficult to judge when welding operation. High temperature aluminum intensity is very low, supporting the fusion pool, easy to weld.
5)aluminum and aluminum alloys can dissolve a large amount of hydrogen in liquid, solid state is hardly dissolved. In the process of welding the solidification and rapid cooling of the welded pool, hydrogen is not overflowing, and hydrogen holes are easily formed. The moisture, welding material and the surface oxide film of the base material and the surface oxide film of the base material are important sources of hydrogen in the weld. Therefore, the source of hydrogen must be strictly controlled to prevent the formation of the air hole.
6)the alloy element is easily evaporated, burned, and the performance of weld is reduced.
7)When the base material matrix metal is modified, the weld heat will reduce the strength of the heat affected zone.
8)aluminum is a facial cube lattice, no hosteem, no phase change during heating and cooling, and the weld grains are very large, and crystal grains cannot be refined by phase change.
Almost various welding methods can be used to weld aluminum and aluminum alloys, but aluminum and aluminum alloys are different from various welding methods, and various welding methods have their respective applications. Air welding and electrode arc welding method, simple equipment, convenient operation. Gas welding can be used to reduce the soldering of aluminum sheets and castings with high welding quality requirements. Electrode of electrode arc welding can be used for rendering of aluminum alloy castings. The inert gas protection (TIG or MIG) method is the most widely used aluminum and aluminum alloy welding method. Aluminum and aluminum alloy sheets can be sold with tungsten argon arc or tungsten argon arc welding. Aluminum and aluminum alloy plates can be sold, argon-helium mixed tungsten gas protection, melted electrode gas protective welding, melted gas protection welding, melted gas protective welding, melted gas protection welding, melted metal protective welding, melted gas protection welding. Molten airtight gas protection welding, pulsed melting gas protective welding applications are increasingly widely widely widely widely (argon or argon / helium mixing gas). Several advanced processes of aluminum alloy welding: stirring friction welding, laser welding, laser - arc composite welding, electron beam welding. A effective solution is proposed for the welding resistance and the alloys that have been considered non-weldable, and several processes have superiority and can be welded to the thick plate aluminum alloy.
The aluminum alloy is widely applied to various welding structural products due to the light weight, high comparison of strength, good corrosion resistance, non-magnetic, formability and low temperature performance. Aluminum alloy replace steel material welding, structure weight It can be reduced by more than 50%.
1)The aluminum alloy welded joint is severely softened, and the strength coefficient is low, which is also the biggest obstacle to the application of aluminum alloy.
2)the aluminum alloy surface is easily produced by a refractory oxide film (Al2O3 has a melting point of 2060 ° C), which requires a welding process of high-power density.
3)Aluminum alloy welding is prone to gas holes.
4)aluminum alloy welding is easy to generate thermal cracks.
5)the linear expansion coefficient is large, easy to produce welding deformation.
6)the thermal conductivity of aluminum alloy is large (about 4 times that of steel), the same welding speed, the heat input is 2-4 times larger than the welded steel.