What is the difference between 201 stainless steel and 304 stainless steel?
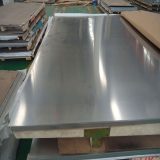
Aluminum alloy ingots are made of pure aluminum and recycled aluminum, and other elements are added in accordance with international standards or special requirements, such as: silicon (Si), copper (Cu), magnesium (Mg), iron (Fe)... Improve the castability of pure aluminum , Alloys formulated with chemical and physical deficiencies. It is suitable for casting and can make castings have good performance.
application:
Aluminum-silicon (Al-Si) alloy, generally the mass fraction of Si is 4%~22%. Because Al-Si alloy has excellent casting properties, such as good fluidity, good air tightness, small shrinkage and low heat tendency, After modification and heat treatment, it has good mechanical properties, physical properties, corrosion resistance and moderate machinability. It is the most versatile and widely used alloy in cast aluminum alloys. The characteristics and applications of common cast Al-Si alloys are as follows:
(1) ZL101(A) Alloy ZL101 alloy has good air tightness, fluidity and thermal crack resistance, moderate mechanical properties, welding performance and corrosion resistance, simple composition, easy to cast, suitable for various castings method. At present, ZL101 alloy has been used for complex parts with moderate load, such as aircraft parts, instruments, instrument casings, engine parts, automobile and marine parts, cylinder blocks, pump bodies, brake drums and electrical parts. In addition, based on the ZL101 alloy, the impurity content is strictly controlled, and the ZL101A alloy with higher mechanical properties obtained by improving the casting technology has been used for casting various shell parts, aircraft pump bodies, automobile gearboxes, etc. Elbow pipes of fuel tanks, aircraft accessories and other parts that are subjected to loads.
(2) ZL102 alloy ZL102 alloy has the best thermal crack resistance and good air tightness, as well as good fluidity, can not be strengthened by heat treatment, low tensile strength, suitable for casting large thin-walled complex parts, mainly Suitable for die casting. At present, this type of alloy is mainly used for thin-walled castings with complex shapes under low load, such as various instrument housings, automobile casings, dental equipment, pistons, etc.
(3) ZL104 alloy ZL104 alloy has good air tightness, fluidity and thermal crack resistance, high strength, good corrosion resistance, welding performance and cutting performance, but low heat resistance, easy to produce small pores, casting The process is more complicated. Therefore, it is currently mainly used to manufacture large-sized sand metal mold castings that bear high loads, such as transmission casings, cylinder blocks, cylinder head valves, pulleys, cover tool boxes and other aircraft, ships and automotive parts.
(4) ZL105 alloy ZL105 alloy has high mechanical properties, satisfactory casting performance and welding performance, better machining performance and heat resistance than ZL104 alloy, but low plasticity and low corrosion stability, suitable for various casting methods. At present, this kind of alloy is mainly used to produce sand and metal casting parts of aircraft and engine under heavy load, such as transmission casing, cylinder block, hydraulic pump casing and instrument parts, and can also be used as bearing support and other machine parts . In addition, the ZL105A alloy developed on the basis of the ZL105 alloy to reduce the impurity content such as Fe, has also been manufactured for high-quality castings under heavy load due to its higher strength and elongation after fracture, such as aircraft crankcases, Valve housings, impellers, cooling jackets, covers, bearing supports and other parts of engines and machines.
(5) ZL106 alloy ZL106 alloy has moderate mechanical properties, good flow properties, satisfactory thermal crack resistance, and is suitable for sand casting and metal casting. At present, such alloys are mainly used for parts with complex shapes and static loads, and parts that require high air tightness and work at higher temperatures, such as pump bodies and water-cooled cylinder heads.
(6) ZL107 alloy ZL107 alloy is suitable for sand casting and metal casting, with good air tightness, fluidity and thermal crack resistance, as well as good mechanical properties and cutting performance. It is mainly used in the production of diesel engine crankcases, piano plates and frames, oil caps and valve handles, cylinder heads and typewriter frames.
(7) ZL108 alloy ZL108 alloy has good casting performance, high strength, small thermal expansion coefficient and good wear resistance. In addition, its high temperature performance is satisfactory, and it is generally used in metal mold casting. At present, this type of alloy is mainly used for components such as pistons of internal combustion engines and lifting pulleys.
(8) ZL109 alloy ZL109 alloy is suitable for metal mold casting, with excellent fluidity, good air tightness and thermal crack resistance, good high temperature strength and low temperature expansion coefficient. Its typical use is to make pulleys, bushings, automobile pistons and diesel engine pistons, and can also be used as lifting pulleys.
(9) ZL110 alloy ZL110 alloy has moderate mechanical properties and good heat resistance, suitable for sand and metal mold casting, alloy density, large coefficient of linear expansion, used to manufacture internal combustion engine pistons, oil nozzles, oil pumps and other parts. However, it should be noted that due to the large thermal expansion coefficient of the alloy, the phenomenon of "cold knocking and hot pulling" may occur when it is used to manufacture pistons.
(10) ZL111 alloy ZL111 alloy has good air tightness and thermal crack resistance and excellent fluidity, high strength, good fatigue performance and bearing capacity, easy welding and good corrosion resistance, suitable for sand mold, Die casting of metal molds. At present, this type of alloy is mainly used for the manufacture of complex, high-load parts, such as castings for aircraft and missiles.
(11) YL112 alloy YL112 is a die-casting alloy with good casting properties and mechanical properties, good fluidity, air tightness and thermal crack resistance. , Lawn mower cover and pneumatic brake castings.
(12) YL113 alloy YL113 alloy has excellent fluidity, good air tightness and thermal crack resistance, and is mainly used for die casting. Typical uses are pulleys, pistons and cylinder heads. It can also be used for die casting of accessories such as automobile engine casings, motorcycle engine casings, and garden tool casings. The international grade is equivalent to the Japanese standard ADC12. It is the most widely used recycled aluminum ingot in the die casting industry.
(13) ZL114A alloy ZL114A alloy has high mechanical properties and good casting properties, that is, high strength, good toughness and good fluidity, air tightness and hot crack resistance, and can cast complex shapes. High-strength castings, suitable for various casting methods, are used for high-strength and high-quality castings, and parts that bear high loads such as aircraft and missile tanks.
(14) ZL115 alloy ZL115 alloy is suitable for sand mold and metal mold casting. It has good casting properties and high mechanical properties, such as high strength and hardness and good elongation. It is mainly used for waveguides and high-pressure valves. , hydraulic pipelines, aircraft pylons and high-speed rotor blades, etc.
(15) ZL116 alloy ZL116 alloy is suitable for sand mold and metal mold casting. It has good air tightness, fluidity and thermal crack resistance, and also has high mechanical properties. It is a high-strength cast aluminum alloy. Typical applications include waveguides, high-pressure valves, hydraulic lines, aircraft pylons, and high-speed rotor blades.
(16) ZL117 Alloy ZL117 is a hypereutectic Al-Si alloy with good wear resistance, low thermal expansion coefficient and good high temperature performance, as well as good casting properties, suitable for metal mold casting, often used as an engine Pistons, brake pads, pulleys, pumps and other parts requiring wear.
(17) YL117 alloy YL117 alloy is equivalent to B390.0 alloy in the United States. It is a hypereutectic Al-Si die-casting alloy widely used in the United States. It has good fluidity, moderate air tightness and good thermal crack resistance. Especially with high wear resistance and low thermal expansion coefficient, it is mainly used for engine blocks, brake blocks, pulleys, pumps and other parts that require wear resistance.
For the Al-Zn alloy, due to the high solubility of Zn in Al, the strength of the alloy can be significantly improved when the mass fraction of Zn is more than 10% in Al. Although this type of alloy has a large natural aging tendency and can obtain higher strength without heat treatment, the disadvantage of this type of alloy is poor corrosion resistance, high density, and prone to hot cracking during casting. Therefore, this type of alloy is currently mainly used to manufacture die-cast instrument housing parts. The characteristics and applications of common cast Al-Zn alloys are as follows:
(1) ZL401 alloy ZL401 alloy has medium casting performance, small shrinkage cavity and hot crack tendency, good welding performance and machinability, high strength in as-cast state, but low plasticity, high density and poor corrosion resistance. At present, ZL401 alloy is mainly used for various pressure casting parts, the working temperature does not exceed 200 degrees Celsius, and the structure and shape of the automobile and aircraft parts are complex.
(2) ZL402 alloy ZL402 alloy has medium casting performance, good fluidity, moderate air tightness, hot crack resistance, good machinability, high mechanical properties and impact toughness in as-cast state, but high density, melting The process is complex and is mainly used in agricultural equipment, machine tools, ship castings, radio devices, oxygen regulators, rotating wheels and air compressor pistons.
The mass fraction of Mg in Al-Mg alloy is 4%~11%. The alloy has low density, high mechanical properties, excellent corrosion resistance, good machinability, and bright and beautiful machined surface. However, due to the complex smelting and casting process of such alloys, in addition to being used as corrosion-resistant alloys, they are also used as decorative alloys. The characteristics and applications of common cast Al-Mg alloys are as follows.
(1) ZL301 alloy ZL301 alloy has high strength, good elongation, excellent machinability, good weldability, anodization, and vibration. The disadvantage is that it has a tendency to microporosity and is difficult to cast. At present, ZL301 alloy is used to manufacture parts with high corrosion resistance, such as frames, supports, rods and accessories, which are subject to high loads, operating temperatures below 150 degrees Celsius, and work in the atmosphere and seawater.
(2) ZL303 alloy ZL303 alloy has good corrosion resistance, good weldability, good machinability, easy polishing, acceptable casting performance, low mechanical properties, cannot be strengthened by heat treatment, and has a tendency to form shrinkage cavities. It is widely used in Die casting. This type of alloy is currently mainly used for parts with medium load under corrosion or in cold atmosphere and parts whose working temperature does not exceed 200 degrees Celsius, such as parts of marine ships and machine casings.
(3) ZL305 alloy ZL305 alloy mainly adds Zn on the basis of Al-Mg alloy, controls natural aging, improves strength and stress corrosion resistance, has good comprehensive mechanical properties, and reduces alloy oxidation, porosity and porosity defects. At present, this type of alloy is mainly used for parts with high corrosiveness requirements, such as parts in marine ships, which withstand high loads, work at temperatures below 100 degrees Celsius, and work in the atmosphere or seawater.