What is the difference between 201 stainless steel and 304 stainless steel?
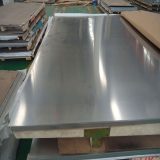
Forging brass is a process of applying pressure to brass bilts by using an forging machine to produce plastic deformation to obtain a forgive product having a certain mechanical properties, a certain shape, and sizes. Forging is one of the two components of forging (forging and stamping). Eliminate the defects such as cast loose generated during smelting process by forging energy, optimize the microstructure structure, while maintaining a complete brass streamline, the mechanical properties of the forged brass are generally better than the same material.
The original state of the forged brass material has a bar, ingot, brass powder and liquid brass. The ratio of the cross-sectional area and the transverse area of the brass before deformation is referred to as forging ratio. Correctly choose forging ratio, reasonable heating temperature and insulation time, reasonable starting temperature and ending temperature, reasonable deformation amount and deformation speed have a big relationship with the quality of reducing the quality of the forging brass.
The general small and medium-sized forged brass is used as a circular or square stick as a blank. The grain tissue and mechanical properties of the base are uniform, good, shape and size, good surface quality, easy to organize mass production. As long as the heating temperature and deformation conditions are reasonably controlled, it is necessary to force brass brass with high forging deformation.
It is easy to produce defects in the process of forging brass: overheating, overflasses; forging cracks; cutting tears; when folded copper alloys, the surface is easy to wrinkle. Therefore, it is more likely to generate folding; the grain is large; stress corrosion cracking.
Cast brass is a cast alloy based on Cu-Zn binary alloy, and its crystallization temperature is small, and the casting performance is better. Compared with tin bronze, the mechanical properties of cast brass are high. In addition, due to a large amount of zinc in brass, there is a low cost. These are the reason why it is widely used in cast brass.
Brass copper sleeves are typical non-ferrous metal castings. Its casting process is of course the same as ordinary non-ferrous metal castings, but some details will be taken differently due to the particularity of the material. The brass copper sleeve has the characteristics of high compared to strength, large stiffness, good shock absorption, good cutting performance. Spare parts for aviation industry, instrumentation, radio technology and transportation.
In addition to understanding the processing flow of brass copper sleeves, it is necessary to master the performance of its performance. When the brass copper sleeve is processed, the control of the cast temperature is very important, generally at least 980 ° C (° C), only suitable for high zinc brass materials. If it is low zinc brass, the cast temperature is high. There are three specific casting processes, namely disappearing mold casting, die casting and sand casting.
After the non-ferrous metal disappear mold casting, the melted alloy is injected into the wax mold, cools solidification, resulting in the desired castings, but a mold can be reused, and the formation of brass copper sleeve. Non-ferrous alloys used to cast brass are one of the casting alloys. It mainly has cast copper alloy, cast aluminum alloy, casting magnesium alloy, etc. Although sand mold is very old, it is also very common, especially small foundation.
In the specific operation of the brass copper sleeve, you must first prepare the mold. It must be recognized that the quality of material is the main factor affecting the quality of the copper. The cast metal is then melted and poured, and the casting is then processed and inspected, including the removal core and the surface of the casting, removes the gate and risks, remove burrs and burrs and other protrusions, and heat treatment, forming, rust rust. And roughing.
Practice has proven that the use of corresponding methods can further increase the hardness of the copper sleeve. For example, a small amount of cobalt is added to the raw material, and the grain size of the cast alloy can be effectively reduced, and the grain shape is changed, thereby increasing the tensile strength and hardness of the alloy, so that the alloy has better plasticity. Copper case castings, colored alloys, copper alloys, aluminum alloys, magnesium alloys, zinc alloys, etc. can be used for casting.
Brass forging and brass casting is two different processing processes.
Brass casting: It is a process of filling the molten brass in a liquid state into a solid state, simply, is to turn the metal fluid having no shape into a shape, and pour the copper raw material. In the sand or mold, the brass workpiece that is solid to be obtained after cooling. For example, it is like playing wax, bought wax (brass raw materials) and then cultivated the wax to liquid, put it into a special mold, which gives something different. (Solid-liquid-solid)
Brass hot forging is the plastic molding of solid state, which is deformed by external force. It is mainly formed by extrusion by high temperature. The grains in the article can be refined and the physical properties are changed. It is like the process of making a cake, you take a small dough, put it in the mold, and make a product of different shapes. Almost is the solid at a high temperature, the shape can become other shapes (solid-solids).
Difference of performance
The brass blanks are plastic deformation, and there is a refined grain, and the cutting fibers are continuous, and therefore often used for blanks of important parts. The brass casting is required to be processed. It does not have a lot of advantages for forging. It is easy to produce a pore during the production process, but it can make a complicated zero, and therefore often used for a blank manufactured by high mechanical properties.