What is the difference between 201 stainless steel and 304 stainless steel?
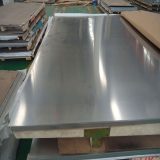
Metal tubular classification methods can be classified according to the use occasion, classified according to production methods, classified by pipe material.
Metal tubes can be divided into pipeline tubes, boiler tubes, mechanical structural tubes, hydraulic and pneumatic systems, oil well pipes, oil and gas delivery tubes, chemical tubes, barrels, and various special use tubes.
Due to the use of applications and the purpose of use, there are different requirements for pipe material, manufacturing methods, and manufacturing quality and cross-sectional structural shape, strength, rigidity, and even corrosion resistance, cold resistance, and heat resistance.
It is mainly divided into two categories: seamless tubing and welding tubes.
The seamless tube refers to the overall closure of the cross-sectional circumferential direction, which is divided into a hot rolling pipe, a cold rolling pipe, a cold drawn and an extrusion tube.
The welding tube is usually soldered by the metal sheet, and the weld is different from the weld direction, which can also be divided into a straight seam welded pipe and a helical welder. The intensity of the spiral welded tube is usually higher than the straight seam welded tube, but the weld length in the same length is increased by 30% to 100%, which is low in production efficiency and high cost.
Under normal circumstances, large-diameter welded pipes are multi-spiral welding.
Due to the purpose and occasion of the use, the pipe is required to have corresponding mechanical properties. According to the material classification, it can be divided into: ordinary carbon tube, alloy steel pipe, stainless steel pipe, bearing steel pipe, weather-resistant steel pipe, corrosion-resistant steel pipe, and various non-ferrous metal tubes.
There are also some special use metal composite tubes and coating tubes.
It can be divided into large, medium and small diameter tubes. According to the relative wall thickness D / t, it can be divided into a special wall (D / T <10), thick-wall tube (D / T = 10 ~ 20), thin-walled tube (D / T = 20 ~ 40) and Polar thin wall tube (D / T> 40), etc.
Circular cross-section and shaped cross-section tubes can be divided.
Under the conditions of wet circumference, the circular cross-sectional area is the largest, and the maximum conveying flow can be obtained with a circular tube delivery fluid. However, the circular cross-section tube also has some limitations, such as the outer shape of the heterogeneous section such as a square or rectangular cross section, as in a planar curved deformation state.
The shaped cross-section tube can be divided into diamond tubes, hexagonal tubes, eight-square tubes, elliptical tubes, and various asymmented cross-sectional tubes.
According to the wall thickness, it can be divided into equality ratio and renaissance tube.
Press the tubing state to be divided into a light tube and a threaded tube. Threaded tubes can also be divided into ordinary threaded tubes, special threaded tubes, etc.
Different from the pressure of pressure, it can be divided into high pressure tubes, medium pressure tubes and low pressure tubes.
There are a variety of methods for achieving curved tubing, most commonly used, on which, on which, there are also special bending methods such as filling, bending, heating, and numerical control.
Each different bending method has unique processes and conditions, as well as the effects of solving a certain bending quality problem.
Conventional unmed bending refers to the use of commonly used tubes without filled chamber temperature, which includes curved, curved, bending, rolling and other bending processes.
On the basis of bending on pure bending, the tubular bending formation is achieved after an axial tension, which is usually divided into a sleeve, and a rotational traction and the like.
All slender forming has a common feature that counteract the inner concave side cutting pressure stress at the time of purely bending, thus suppressing the wall thickness and wrinkles of the elbow, but inevitably increase the curved side The possibility of wall thickness and even pulse.
It is a simplified working principle of common sleeve forming. When the pipe is pulled, the tube blank is secured by three horizontal support rollers and secured to the arm bonded to the rotary, and the arm is rotated to produce bending deformation.
When the bend is formed, the distance from the support roller and the chuck and the wheel axis can be changed, and the radius of curvature can be changed. If the heating device is attached to the bending area before the tube blank, for example, the medium frequency induction current is preheated to the tube blank, and the plastic deformation capability can be improved, and the heated pull-bend mold is improved.
Rotary traction bending, each of the bending works has a groove that matches the outer shape of the pipe, and the cross-section curve length is slightly smaller than the semicircle of the tube blank, and is used to clamp or press the billet when bending, and the rotary bend can be changed. radius.
The tube blank is pressed against a rotary bend that can rotate around the axis, and the traction mold is rotated on the arc track of the fixed radius of the rotary bending direction, and the billet is rotated in radial direction and Rotating the bending formation with the rotary bending mode under the action of the pressing block.
Since the curved outer convex side tube blank is increased, the tensile is bent.
At present, most of the elongation equipment and CNC bending machines in production are similar to the rotation traction.
The compression bending is corresponding to the stretching bending, which is a tube bending formed by an additional or derived axial thrust to the bending moment.
Additional axial thrust can reduce or counteract the role of the bending outer convex side, thus suppressing the thickness of the elbow wall thickness or cracking, but at the same time, the tube wall is increased by increasing the curved inner concave side Wrinkle.
Pipe compression bending is mainly divided into: curved, rotary compression bending and axial force curvature.
The pipe pressure is similar to the sheet V shape, which can be used to bend the shape of a straight pipe section and a small diameter elbow. The bending die and the support roller have a working groove having the same tube diameter and slightly less than the semi-circular, which is fixed to the push rod and has a certain bending radius, and rolls the billet between the two side support rollers. Replacing the bending can change the length of the pipe, the size of the two-curved internal angle is determined by the bending mode.
The tube is increasing and has a high efficiency and a simple mold adjustment. A disadvantage is that the inclination of the bending force is concentrated between the two support rollers, and the billet is easily distorted at the initial contact of the bend, affects the quality of the bending.
The rotary compression bending and the rotary traction bend is also similar in the form, but the curved deformation mechanism of the pipe is different.
As shown in the figure below, when bending, the slide press or roller is applied to the tube blank, and the axial core of the fixed bend is rotated, and the straight tension is gradually subjected to fixed bending grooves under tangential friction. Forming and bending.
Different from the tube rotary traction bending, the curved deformation zone generates between the sliding press mold and the fixed bending, and the surface of the outer convex side tube is always in the common effect of radial pressure and tangential friction, which gives some extent Gram relative to alleviate the amount of deformation of the curved outer convex side tube blank.
As shown in the figure below, the model is composed of two semi-molds in the curved plane. The tube blank is forced to bend the molded cavity after the pressing axial thrust is complicated, and the bending deformation process in the mold is complicated, except for the bending moment, and is also operated by axial thrust and its operation. The opposite friction is opposite.
Unlike ordinary bending, the wall strain neutral layer may move toward the outer side, so that the outer wall thickness is thinned.
The pipe push should generally require a relative wall thickness to 0.06 to avoid the inside of the elbow, wrinkles or distortions. In order to reduce friction, it is often necessary to lubricate the tube blank or bend mold cavity. For thin-walled elbows, usually use core push bends to avoid debarning.
In addition to the above methods, there are also winding, rolling, and the like. Most of these methods are difficult to meet stringent bending accuracy and bending quality, so it is commonly used for tubular members with high-dimensional precision requirements.
The pipe is bent is a typical elongated pipe process, usually divided into handmade bending and wonderful bending.
There is some similar to the rotary compression bend, but rolling friction when the roller working groove is between the surface of the tube blank.
When bending, one end of the tube blank is sandwiched, and the side press wheel is pressed against the bending groove profile and rotates together from the bending, and the chuck is rotated together with the tube.
The tubular rolling is usually used in thick wall tubes.
Between three or four or more rollers, each roller is slightly larger than the outer diameter of the tube, and the section peripheral length is slightly smaller than the groove of the semicircle, each roller rotates in different directions and moving positions. The tube is rolled to form a certain curved shape.
Multi-rolling can improve the bending accuracy of the pipe, reduce the bending cross-section distortion, and improve the homogeneous bending of the tube, sometimes it can be used for thin-walled tube bending forming.