What is the difference between 201 stainless steel and 304 stainless steel?
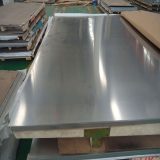
The internal folding defect of the steel pipe refers to the existence of the overlapping layer fused with the whole metal on the inner surface of the steel pipe, or the head of the steel pipe, or the whole steel pipe, either regularly or irregularly. The steel pipe with this defect can be used for grinding if it is light, and it can be downgraded or scrapped if it is serious. The main influencing factors are:The relationship between continuous casting billet quality and inward folding.
The reason for the formation of shrinkage cavity is that in the process of continuous casting, at the solidification end of the liquid phase cavity, the central solidification speed of the slab is very different from the surface solidification speed, which will cause the difference between the central shrinkage and the surface shrinkage. The center of the shrinkage is fast. The liquid phase cavity at the end of solidification is narrow and the viscosity of molten steel is large. If the volume void caused by the center shrinkage cannot be replenished in time, a center shrinkage cavity will be formed in the center of the slab.
If the columnar crystals are small and dense; the central shrinkage cavity is small and there are intermittent concentrated looseness in the center of the slab, so that the end shrinkage cavity is relatively short even if it is oxidized when the slab is heated, and the formed inward folds are concentrated in a very short range of the tube end. , the vast majority can be cut off. Some billets have no central shrinkage cavity at all.
In addition, the slow cooling treatment of the tube billet, especially the slow cooling of the alloy steel billet, the reduction of the inner fold is more obvious.
The size of the roll speed is designed according to the material of the billet, elongation coefficient, slip coefficient and roll diameter. The results show that the inner fold is more likely to be formed at high rotation speed, and the inner fold is correspondingly reduced when the rotation speed is reduced. The main reason is that increasing the rotational speed of the rolls will lead to an increase in slippage, that is, a decrease in axial efficiency, an increase in the number of rotations of the tube blank in the biting section, and an increased possibility of forming inward folds. The test results confirm that the adjustment direction of the puncher is: using a large bite angle, the slip of the tube blank decreases with the increase of the bite angle, and the reduction of the slip can reduce the number of rotations required for the tube blank to bite. Based on the experience of foreign manufacturers, the forward efficiency is the best when the bite angle is 10 to 12 degrees.
The effect of the speed-up ratio is that the roll rotates at a low speed, which is conducive to the smooth bite of the tube blank, and the high-speed rolling and high-speed steel throwing after the bite. It is generally set at 30%, and 40% or 45% is often used in production depending on the wear of the roll. The experimental results show that the amount of inflection produced by piercing with a speed-up ratio of 30% is lower than that produced by piercing with a speed-up ratio of 45%. Inward fold. The theoretical basis is that in the low-speed biting stage and the high-speed rolling stage, the speed difference between the two is small, and the deformation conditions of the slab are similar. That is to say, the metal flow can smoothly transition from low speed to high speed. If the speed difference between the two is large, the metal deformation will fluctuate and it is easy to produce large inward folding. This inflection is often found at 400 to 500 mm from the front end of the capillary.
The function of the pre-rotation of the plug is also conducive to the biting of the tube blank. The pre-rotation speed value is generally set at 70% of the tube blank rotation speed and the rotation direction is consistent. The test results show that the inflection amount produced by 20% pre-rotation speed is significantly lower than 100% set rotation speed.