What is the difference between 201 stainless steel and 304 stainless steel?
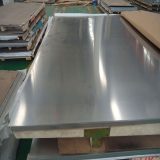
With the improvement of people's quality of life, the requirements for product aesthetics and quality are also constantly improving. More and more consumer products are made of alloy materials. Metal materials give people a sense of high-end, strong and durable quality, while traditional plastic shell products are gradually being labeled as "cheap" and "low-quality" in consumers' minds.
For consumer products, commonly used alloy materials are aluminum alloys, zinc alloys and magnesium alloys. Titanium alloys are commonly used in the medical field due to their good biocompatibility. Let's take a look at the characteristics of these alloy materials and make a comparison.
Physical properties comparison:
Of the four alloys, titanium is the hardest and has the best strength. In terms of hardness, titanium alloys are much harder than the other three alloys. In terms of tensile strength, titanium alloys are stronger than zinc alloys, followed by magnesium alloys, and aluminum alloys have the lowest strength.
Strength and hardness comparison:
However, in terms of product structure design, weight also needs to be considered. If the specific gravity is considered as progress, the specific strength of zinc alloy is the smallest due to the highest density. Titanium alloys and magnesium alloys have high specific strength, but titanium alloys are expensive and have poor workability. Therefore, magnesium alloys are mostly used in structural parts that need to comprehensively consider weight and strength.
The ingredients are directly found by Du Niang, which is listed here without a lot of space. The density of aluminum alloy is 2.63~2.85g/cm, high strength (σb is 110~270MPa), the specific strength is close to that of high alloy steel, the specific stiffness exceeds that of steel, it has good casting performance and plastic workability, and good electrical conductivity , thermal conductivity, good corrosion resistance and solderability.
The fluidity of die-cast aluminum alloy is relatively good, and the melting point is 660 °C.
Zinc alloy has low melting point, good fluidity and easy fusion welding. According to the manufacturing process, it can be divided into cast zinc alloy and deformed zinc alloy. Cast zinc alloy has good fluidity and corrosion resistance, and is suitable for die-casting instruments, automobile parts casings, etc. Deformed zinc alloys have good plasticity and ductility, and are mainly used as battery casings, printing boards, roof panels and household hardware. The output of cast alloys is much larger than that of deformed alloys. For structural parts of fast-moving consumer goods, deformed alloys are rarely used. Therefore, the following is only for die-cast zinc alloys.
The density of zinc alloy is 6.3~6.7g/cm, the tensile strength σb is 280~440MPa, the melting point is low, it melts at 385℃, and it is easy to die-cast.
Magnesium alloys are alloys based on magnesium and other elements. The main alloying elements are aluminum, zinc, manganese, cerium, thorium and a small amount of zirconium or cadmium. At present, the most widely used is magnesium-aluminum alloy, followed by magnesium-manganese alloy and magnesium-zinc alloy. Because of its excellent casting, extrusion, cutting and bending properties, magnesium alloys can be widely used in the fields of automobiles, electronics, textiles, construction and military.
The melting point of magnesium alloy is 650 ℃, the melting point is lower than that of aluminum alloy, and the die-casting performance is good. The tensile strength of magnesium alloy castings is comparable to that of aluminum alloy castings, generally up to 250MPa, and up to more than 600MPa.
Magnesium alloys have low density (about 1.8g/cm3) and high strength. Magnesium alloy is the lightest metal structural material, with a specific gravity of only 1.8, which is 2/3 of aluminum and 1/4 of iron, and its specific strength is as high as 133, which makes magnesium alloys can be used as high-strength materials. The specific strength of high-strength magnesium alloys is even comparable to that of titanium.
Titanium is non-toxic, light in weight, high in strength and has excellent biocompatibility. It is an ideal medical metal material and can be used as implants in the human body. In the United States, five β-titanium alloys have been recommended to the medical field, namely TMZFTM (TI-12Mo-^Zr-2Fe), Ti-13Nb-13Zr, Timetal 21SRx (TI-15Mo-2.5Nb-0.2Si), Tiadyne 1610 (Ti-16Nb-9.5Hf) and Ti-15Mo, suitable for implantation into the human body, such as artificial bones, vascular stents, etc.
The biocompatibility of TiNi alloys is very good, and there are quite a few medical examples of utilizing its shape memory effect and superelasticity. Such as thrombus filters, spinal rods, orthodontic wires, vascular stents, bone plates, intramedullary needles, artificial joints, contraceptives, heart repair components, micro-pumps for artificial kidneys, etc.