What is the difference between 201 stainless steel and 304 stainless steel?
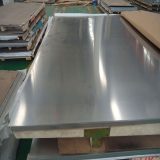
Forged raw materials are ingots, rolled materials, extruded materials and forging blanks. The rolling, extruded, and the forging blanket is a semi-finished product that is rolled, squeezed, and forged. In general, the occurrence of internal defects or surface defects in the ingot is sometimes inevitable. In addition, improper forging process during the forging process, eventually leading to defects in the forg. Next, briefly introduce some of the common defects in forgings.
Surface cracks occur more on rolling bars and forged bars, generally in linear shape, and the main deformation direction of rolling or forging. There are many reasons why this defect, such as the subcutaneous bubbles in the ingot, elongate in the deformed direction, exposes the surface and develops in the interior. In addition, as in rolling, the surface of the blank is scratched, and the stress is caused when it is cooled, so that it may be fracted along the scratch. This crack is not removed before the forging, and it is possible to extend the crack crack when forging.
The reason for folding is to form when the metal blank is in the rolling process, due to the uncertainty of the tank on the roll, or the burrs generated by the groove grinding surface are involved in rolling, forming and material surface into a certain inclination angle. Band. For steel, there is an oxide sand in the flask, and there is a de-carbon. Folding If you don't get it before the forging, it may cause a forgings fold or crack.
Sparking is a peeling film in a partial region of the surface of the rolling.
The formation of the scar is due to the casting of the steel fluid in the surface of the steel, and is pressed into a film when rolling, and is attached to the surface of the rolled material. After the forging, the forging is cleaned, and the film will peel off and become the surface defect for forgings.
The characteristic of the layered fracture is that the fracture or section is broken and the bark is similar.
The layered breaks occur in alloy steel (chromium nickel steel, chromic nickel tungsten steel, etc.), and there is also found in carbon steel. The generation of such defects is due to defects such as non-metallic inclusions, dendrites, dendritic segregation, and pore loosening in the steel, which is elongated in the rolling direction during the forging and rolling, so that the steel material is laminated. If the impurities are too much, forging is a risk of hierarchical rupture. The closer the layered break, the worse the plastic toughness of the steel, especially the lateral mechanical properties, so steel such as obvious layer-like defects are unqualified.
The bright line is a thin strip of reflective ability to crystallize in the longitudinal fracture, mostly throughout the entire fracture, mostly generated in the axial portion.
The bright line is mainly due to alloy segregation. The slight bright line has little effect on mechanical properties, and severe bright lines will significantly reduce the plasticity and toughness of materials.
Non-metallic inclusions are mainly formed by smelting or casting the chemical reaction between the components or between the metal and the furnace gas during molten or cast steel water. Further, in the metal smelting and casting, the inclusions can also be formed due to the refractory material falling into the steel liquid, which is also formed by the clamp. On the cross section of the forging, non-metallic inclusions can be dotted, sheet-like, chain or bulk distribution. Severe inclusions can easily cause cracking of forgings or reduce the performance of materials.
Carbide segregation is often present in a high carbon-containing alloy steel. It is characterized in that there are more carbide aggregation in the local area. It is primarily caused by dental eutectic carbide and secondary mesh carbide in steel, which is not broken and uniform distribution during billet and rolling. Carbide segregation will reduce the forging deformation properties of steel, which can cause cracking for forgings. Forgings heat treatment, it is easy to top well, overhever and quenching.
Aluminum alloy oxide films are typically located on the web of the die forgings and near the mold surface. A fine crack in low-altitude tissue, in the high-powered tissue, the characteristics of the fracture can be divided into two categories: one, flat sheet shape, color from silver gray, light yellow until brown, dark brown Second, it is a distinctive point with a flash.
The aluminum alloy oxide film is formed by the oxide film formed in the molten melt surface of the molten casting and the water vapor or other metal oxide interaction in the atmosphere.
The oxide film in the forgings and moldings has no significant effect on longitudinal mechanical properties, but the mechanical properties of the height direction have a large effect, it reduces the high direction strength performance, especially the elongation, impact toughness, and high direction of height direction. Corrosion performance.
The main feature of the white point is that the longitudinal fracture of the billet is circular or elliptical, which is small crack on the lateral fracture. The size of the white point is different, the length is from 1 to 20 mm or longer. White points are common in alloy steels such as nickel-chromium steel, nickel-chromium molybdenum steel, and there are also discovery in ordinary carbon steels and is hidden in internal defects. The white point is produced under the common action of hydrogen and phase transition and the common action of thermal stress. When the amount of hydrogen containing hydrogen containing is more easily generated when the heat pressure processing is reduced (or forging heat treatment).
Forgings with white-point steel, it is prone to cracks during heat treatment (quenching), sometimes even blocking. White points reduce the strength of the plasticity and parts of the steel, it is the stress concentration point, which is like a sharp cutter, which is easy to become fatigue cracks under the action of an alternating load, resulting in fatigue damage. Therefore, it is absolutely not allowed in the forging raw material.
The crude crystal ring is often the defects present on aluminum alloy or magnesium alloy extruded bars.
The extrusion of the aluminum and magnesium alloy supplied after heat treatment, often has a crude crystal ring in the outer layer of its circular section. The thickness of the crude ring is gradually increased by the beginning ends of the extrusion. If the lubrication conditions are good when the extrusion is excellent, it can be reduced or avoided after heat treatment. Conversely, the thickness of the ring will increase.
The cause of the crude crystal ring is related to many factors. However, the main factor is the friction generated between the metal and the extruded cylinder due to the extrusion process. This friction causes the outer layer of the extruded bar cross section to be much larger than the fragmentation of the grains at the center of the bar. However, due to the influence of the wall, the temperature is low, and the crystal grains that are not recrystallized when the quench is heated, and the crystal grains which have been recrystallized when the quench is heated. ring.
Billet forging with crude crystal ring is easily cracking, such as the crude crystal ring remains in the forgings, and the performance of the part will be reduced.
The shrinkage residual is generally due to the concentrated shrinkage of the steel ingredients, and remains inside the steel.
Interpose of intensive inclusions, loosening or segregation in the residual area of the shrinking. There is an irregular wrinkle gap in a low degree of transverse. It is easy for forging or heat treatment to cause cracking.
When the cut is in a sawing machine or punch, since the rod is not pressed, the amount of tilt of the blank end surface with respect to the longitudinal axis exceeds the predetermined license value. Severe cutting may form fold during the forging process.
During the cutting machine or punch, due to the clearance between the scissors or the cutting blade, it is too large or due to the sharp edge, the blank has been curved before being cut, and the part metal is squeezed or molded. In the gap, the end of the mouth is formed.
There is a glitch-type blank, which is easy to cause local overheating, overheating, and forging when heating.
When the clearance is applied to the shearing bed, since the gap between the scissors is too small, the lower crack is not coincident, resulting in a secondary shear, and the part of the end metal is pulled off, and the end face is concave. Such blanks are easily folded and cracking.
When the cold shear is broken alloy steel and high carbon steel bars, cracks are often discovered at 3 to 4 hours after shearing. It is mainly due to the large unit pressure of the blade, so that the blank of the circular section is pressed into an elliptical shape, and a large internal stress is generated in the material. The flattened end face strives to restore the original shape, and the cracks are often occurred under the injection of the internal stress. Hardness is high, hardness unevenness and material segregation are also easy to produce shear cracks.
A blank with end cracks, cracks will be further expanded during forging.
The gas cut crack is typically located at the end of the blank, and is caused by tissue stress and thermal stress when the gas cutting raw material is not preheated.
A blank of gas cutting cracks will be further expanded during forging. Therefore, it should be pre-cleared before the forging.
When the lathe is filled with, the center portion of the end surface of the rod tends to leave a cylinder. During the forging process, since the clearance of the cylinder is small, the cooling is very fast, and thus the plasticity is low, but the part is large, the cooling is slow, and the plasticity is high. Therefore, in the sectional mutation transfer, the part of the stress is concentrated, and the difference between the two parts is large, so the surrounding of the cylinders is easily calendering under the action of hammering force.
(1) The medium affects the defects caused by changes in the outer layer of the blank, such as oxidation, decarburization, carbon-free and sulfur sulfur, and copper, etc.
(2) Defects caused by abnormal changes in the internal tissue structure, such as overheating, overbur, and unmissive, etc .;
(3) Since the temperature is unevenly distributed inside the blank, it causes internal stress (such as temperature stress, tissue stress), and the like.
Large crystal grains are usually caused by insufficient excessive forging temperature and deformation degree, or the final temperature is too high, or the deformation is caused by the deformation zone. The aluminum alloy is too large, forming a texture; the high temperature alloy deformation temperature is too low to form a mixed deformation tissue, which may also cause coarse crystal grains. The crystal grains will reduce the plasticity and toughness of the forgings, and the fatigue performance is significantly reduced.
Small grains is unevenly means that the grains of certain parts of the forgings are particularly thick, and some parts are smaller. The main reason for producing crystal grains is that the deformation unevenness of the grains is not uniform, or the deformation of the grain crush is different, or the deformation of the local area is deformation zone, or the high temperature alloy is partially processed, or the local grains when heat is heated. Rough. Heat resistant steel and high temperature alloys are particularly sensitive to crystal grains. The loss of grains will make the long-lasting performance and fatigue performance of the forgings.
Due to the deformation of the temperature, the temperature is too low or the deformation speed is too fast, and the cooling of the re-crystallization may cause the re-crystallization, which can still be partially reserved inside the hot forging forging. Deformation tissue. The presence of such an organization increases the strength and hardness of the forging, but reduces plasticity and toughness. Severe coldness may cause forging.
Forging cracks are typically caused by greater tensile stress, cutting stress or attachment stress during forging. The fragmentation occurs is usually a portion where the billet stress is the most stress and the thickness. If there is a microcrack in the surface of the blank, or the tissue defect in the blank, or the thermal processing temperature is not properly lowered, or the deformation speed is too fast, the degree of deformation is too large, and the plastic pointer that exceeds the material allowed, then withdrawal, Cracks may occur in untenas, punching, renovation, bending, and extrusion.
Forging cracks are shallow turtle cracks in the surface of the forgings. Such defects are most likely to produce such defects (eg, unfilled projections or bend) in the sleeve forming.
During the cooling process of forging forging, the internal heat stress is produced inside the forging due to excessive cooling velocity, or may cause greater tissue stress due to tissue transitions. If these stresses exceed the strength limit of the forgings, the forgings produce smooth and elongated cooling cracks.
When the amount of steel having high carbon is forged, if the stop forging temperature is high, the cooling speed is too slow, it will cause the carbide to be a mesh in the crystal boundary. For example, the bearing steel is cooled in 870 to 770 ° C, and the carbide is precipitated along the crystal.
Forging mesh carbides can cause quench cracks during heat treatment. In addition, it also causes the performance of the part to deteriorate.
Forging due to improper hardness of heat treatment after the forging, the hardness is not enough: 1 The quenching temperature is too low; 2 quenching heating time is too short; 3 tempering temperature is too high; 4 multiple heating causing severe deprophy from the surface of the forgings; 5 steel The chemical composition is unqualified.
Forging due to improper hardness of the heat treatment process, it is:
① Cooling after normal fire is too fast;
② normal fire or temper heating time is too short;
③ steel chemical components are unqualified.
The main reason for the unevenness of the forging causes the heat treatment process, for example, the amount of load is too large or the holding time is too short; or heating causes partial de-carbon production of forgings.
Excessive forging acid washing will make the surface of the forging porous porous shape. This defect is mainly due to the depth of acid and the residence time in the acid wash tank is too long, or the acid solution remains on the surface of the forging surface due to the cleaning of the forging surface.
If there is a large residual stress after forging martensite, there is a large residual stress, it is easy to produce a thin web corrosion crack on the surface of the forgings. If the organizational coarse brilliant formation is formed.
① Product precision (net parts development)
② Rationalization of the process (with minimum investment costs and production costs as the principle of consolidation and application)
③ Automation, save time