What is the difference between 201 stainless steel and 304 stainless steel?
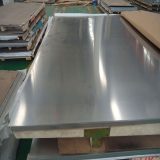
Simple and complex metal parts are spread all over the world. Many metal products are manufactured using metal forging processes from complex aerospace components, and many metal products are made of metal forging process. This process makes materials enough to be strong enough, enough to win the task of hand.
Forging, it is one of the metal pressure machining methods. Refers to a process of changing the shape of a metal raw material using pressure to obtain a process of hardware having a certain mechanical properties, a certain shape, and size.Typical metals used during the forging process include carbon, alloy steel, aluminum, stainless steel and copper alloys. Choosing a suitable metal ensures that the forging product meets the design specifications and produces necessary quality.
The manufacturer is forged by using a thermally binding compression method such as rolling, hammer and pressing) until the metal is formed. Forging metals have different methods, each method provides different advantages for the production line. Common methods may include:
Falling forging. Falling forging involves molding metal molds into the desired shape using a hammer and mold. Falling forging can use open or closed molds depending on the details of the project.
Stamping forging. Pressure forging uses multiple molds instead of using a mold for use with a hammer. Pressure is continuously applied using hydraulic or mechanically until the metal is formed.
Rolling. It is also known as rolling molding, and the roll forging involves compressing the metal rod into the desired shape using a cylindrical or semi-cylindrical roll with a shaped groove.
The above method is often combined with the thermal phase to make the metal more durable. Hot forging allows manufacturers to change metal mechanical and structural properties to provide certain quality, such as tensile strength or ductility. This method can also help further remove impurities that may cause voids or cracks in the metal.
Hot forging is forged for metal above the recrystallization temperature. Improve temperature can increase the plasticity of the metal, which is conducive to improving the inherent quality of the workpiece, making it difficult to crack. High temperatures can also reduce metal deformation resistance and reduce the tonnage required for forging machinery. However, hot forging process, poor workpiece, the surface is not smooth, and the forgings are easily oxidized, deprophydric and burn. When the workpiece is large and thick, the material strength is high, the plastic is low (such as the rolling of the ultra-thick plate, the pull length of high carbon steel bar, etc.), with hot forging. When metal (such as lead, tin, zinc, copper, aluminum, etc.) has sufficient plasticity and the amount of deformation is not large (such as in most stamping processing), or the total amount of deformation and the forging process used (such as extrusion, Radial forging, etc.) facilitates the plastic deformation of the metal, often uses hot forging, and uses cold forging.
The temperature range of the initial forging temperature and the forging temperature should be as large as possible in order to complete as much forged work as possible by one heating. However, high-starting temperature can cause excessive growth of metal grains, forming overheating, thereby reducing the quality of forgings. When the temperature is close to the melting point of the metal, the low melting material is melted and the inter-crystal oxidation occurs, resulting in overbur. Excessive burning billets often break during the forging process. General hot forging temperature is: carbon steel 800 ~ 1250 ° C; alloy structure steel 850 ~ 1150 ° C; high-speed steel 900 ~ 1100 ° C; common aluminum alloy 380 ~ 500 ° C; titanium alloy 850 ~ 1000 ° C; brass 700 ~ 900 ° C.
Cold forging is lower than the recrystallization temperature of metal forging, commonly referred to as normal temperature cooling, which will be higher than room temperature, but does not exceed the forged recrystallization temperature called warm forging. The temperature forging precision is higher, the surface is smoother, and the deformed resistance is not large.
Alternatively cold-molded artifacts are highly accurate, the surface is smooth, and the processing is less process, easy to automate production. Many cold forging and cold press parts can be used directly as part or products without cutting. However, in cold forging, due to the low plasticity of the metal, it is easy to crack, deformation resistance, and the large tono forgings are needed and the stamping machine is required.
Advantages of hot forging:
If the processing is completed, the temperature of the forging material is still much higher than the recrystallization temperature, and the grain has a longer period of time, which will result in a thicker grain, which can increase the toughness of the fracture toughness (lower crack expansion rate).
Disadvantages of hot forging:
(1) Because of high temperature operation, the risk of safety and material safety is large.
(2) The material is easily oxidized at high temperatures, producing oxidized skin, causing surface area, finishing, and flatness.
(3) After hot forging, the forging material has a cold shrinkage during the cooling process, affecting the accuracy of the forgings.
(4) The equipment and maintenance costs required for high temperature operation are high.
Advantages of cold forging:
(1) Forgings are not easy to produce oxidized skin, and the surface finish is better.
(2) The precision of the forgings is better.
(3) Processing hardening (strain hardening) during processing, can increase strength and hardness.
(4) The metal fibers of the forging can be enabled to obtain specific directionality.
(5) Do not need to heat treatment, so that pollution is minimized.
(6) Do not need to heat the cost, reduce production costs.
Disadvantages of cold forging:
(1) The plasticity and toughness of the forgings are lowered, and the subsequent processing is unfavorable.
(2) The desired deformation force is less forged.
(3) The inside of the material produces residual stress.
(4) Metal grains will deform or crush.
(5) Directionality in the process of processing may not be conducive to future products.