What is the difference between 201 stainless steel and 304 stainless steel?
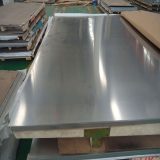
Extrusion processing refers to putting the pre-prepared billet into an extrusion cylinder and applying pressure to extrude the material from the opening of the container. During extrusion, the material is in a state of unequal three-direction compressive stress, and the strain state is axial elongation.
Extrusion is mainly used to produce non-ferrous metal pipes, rods and profiles with complex cross-sectional shapes, precise dimensions and high surface quality, and can also be used to produce steel products such as seamless steel pipes.
There are many classification methods for extrusion. According to the metal temperature during extrusion, it can be classified into hot extrusion and cold extrusion; according to different billets, it can be divided into ingot extrusion, billet extrusion, powder extrusion and liquid metal extrusion; The extruded metal material can be divided into ferrous metal extrusion and non-ferrous metal extrusion; according to the metal flow direction, it can be divided into positive extrusion, reverse extrusion and lateral extrusion.
Forward extrusion and reverse extrusion are classified according to the flow direction of the metal and are the most commonly used classifications.
● Forward extrusion
The metal flows in the same direction as the extrusion rod moves. During the extrusion process, there is relative sliding between the metal ingot and the inner wall of the extrusion cylinder, and there is a large external friction force, so the extrusion force is large.
● reverse extrusion
The metal flows in the opposite direction of the movement of the extrusion rod. There is no relative movement between the metal ingot and the extrusion cylinder, so there is no external friction.
Reverse extrusionn has less extrusion force and less metal scrap than forward extrusion.
● Lateral extrusion
During transverse extrusion, the die is placed at 90° to the axis of the metal blank, the force acting on the blank is consistent with the axis, and the extruded product flows out of the die hole in a direction of 90° to the extrusion force.
The longitudinal properties of the transversely extruded products vary less, and the material properties are improved.
Classification by metal material:
According to the extruded metal material, it can be divided into ferrous metal extrusion and non-ferrous metal extrusion, among which non-ferrous metal extrusion is the most widely used.
Non-ferrous metal extrusion can be subdivided into: light non-ferrous metal extrusion, heavy non-ferrous metal extrusion and rare and precious metal extrusion.
Light non-ferrous metals: aluminum, aluminum alloy, magnesium alloy extrusion products, various aluminum profiles, wire billets, pipes, etc. for construction.
Heavy non-ferrous metals: lead, copper, zinc, nickel, etc. Among them, copper and copper alloys are the most widely used.
Rare and precious metals: titanium alloy, tungsten, molybdenum, tantalum, niobium, etc.
Classification by product section:
Divided into pipes, rod profiles, wire blanks, etc.
Classification by extrusion temperature:
Generally divided into hot extrusion, warm extrusion and cold extrusion.
In the metallurgical industry, hot extrusion is mainly used, and in the machinery industry, cold extrusion is mainly used.
In the field of metal plastic deformation, compared with rolling, drawing, forging and stamping, extrusion method appeared later and belongs to a new processing technology. With the innovation of technology and the improvement of requirements, more and more kinds of metals can be produced by extrusion, but extrusion also has its own advantages and limitations.
Advantages of extrusion:
The extrusion method mainly produces pipes, bars, profiles and wire blanks. Compared with other metal processing methods, its advantages are as follows:
1) It has a stronger three-dimensional compressive stress state diagram than rolling, and the metal can exert the maximum plasticity, so the extrusion method can process metals that cannot be processed by rolling and forging. For brittle materials such as tungsten, molybdenum, etc., the extrusion method can also be used to open the billet, and then processed by other methods.
2) The extrusion method can produce products with complex cross-sections, while other processing methods are difficult or impossible to handle, and the economic cost is high.
3) The extrusion method has excellent flexibility. By changing the hole die, the same equipment can produce various types and specifications of products. Therefore, it is very suitable for the production environment of small batch, multi-variety and multi-specification.
4) The product size is accurate and the surface quality is high. Due to their high surface quality and dimensional accuracy, most extruded products can be used without further processing.
5) It is easy to realize production automation and closure. It greatly reduces the dependence on personnel on the processing site, and does not require manual intervention in special harmful production environments.
Disadvantages of extrusion:
1) The loss of fixed scrap of metal is large. Because the pressure surplus and the extrusion tail are left at the end of the extrusion, there is a loss of the perforated material head when the pipe is extruded, so the cutting loss is large and the metal yield is low.
2) The processing speed is slow. The extrusion process is a closed environment, and a large amount of deformation heat is generated, and the heat cannot be dissipated in time. Therefore, it is necessary to control the processing temperature by controlling the processing speed to avoid the temperature being too high beyond the bearing capacity of the metal.
3) The organization and properties of the length and the direction of the section are not uniform enough. This is due to the uneven deformation of the inner and outer layers and the front and rear ends of the ingot during extrusion.
4) The mold consumption is large. During the processing, the stress is large, the temperature is high, and the life of the extrusion die is shortened. The molds are all expensive high-grade heat-resistant alloy steel.
Although the extrusion method has its own limitations, it is used in the production of pipes and profiles with complex cross-sections and thin wall thicknesses; ultra-thick-wall pipes with a ratio of diameter to wall thickness close to 2; brittle non-ferrous metals and alloys. The only viable method of press working.