What is the difference between 201 stainless steel and 304 stainless steel?
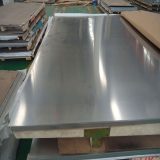
Aluminum profiles are mentioned, everyone will think of all kinds of aluminum profile frames, equipment hoods, pipeline tables, etc. made of aluminum profiles. So why do these frameworks use aluminum profiles? Because the surface of the aluminum profile is treated with anodic oxidation, it is elegant and corrosion.
Anodizing is an aluminum and its alloys form a layer of oxide film on an aluminum article (anode) under the action of the external current, and its alloy is formed in the corresponding electrolyte and a particular process.
The anodizing of aluminum is an electrolytic oxidation process, during which the surface of the aluminum and aluminum alloy is usually converted into a layer of oxide film, which is protective, decorative film, and some other functional characteristics. The anodization of aluminum from this definition, only the process of generating an anodized film.
First, has decorative. After the aluminum profile passes through anodized treatment, the surface forms a layer of protective film, and the protective film is highly translucent. If there is a dye with other colors, a colored oxide film is formed. There is a good decorative and anti-corrosion resistance to reach the role comparable to the tile.
Second, there is no conductivity. We know that the aluminum profile itself is electrically conductive, and many charged frames cannot be used. However, after the aluminum profile is treated with anodized, it does not conduct electricity. Therefore, many charged devices can be made with aluminum profiles, which can be partitioned to reduce current damage to property and articles. Aluminum and aluminum alloy articles have a large resistance after the oxide film obtained after the anodized oxide, so it has a certain role in improving the electrical insulation of certain products, and can prepare a dielectric layer of the capacitance with an anode oxidation. Aluminum oxide prepare an insulating layer surface.
Third, with anti-corrosion resistance. Since the membrane layer obtained by the anode oxidation is sufficient stability in the atmosphere, the oxide film on the aluminum surface can be utilized as a protective layer. The aluminum is dense, the oxide film obtained by the anode oxidation is dense, and the corrosion resistance is good; the pores of the oxide film obtained from the sulfuric acid solution are large, and the industrial aluminum profiles are thicker, and the adsorption capacity is very strong. If appropriate filling is closed, its corrosion resistance is also very good. It is particularly pointed that the anode oxidation of the chromate is particularly suitable for the anodized treatment of the riveting member and the welded member.
Aluminum workpiece →racking →Deanify → rinsing →Alkaline degreasing → rinsing → desmutting →rinsing → anodic oxidation → rinsing → deionized water →colouring→ rinsing → deionized water →sealing → rinsing →under the plating rack.
In order to overcome the defects of aluminum and aluminum alloy surface hardness, wear resistance, etc., expand the application range, extend the service life, and surface treatment techniques become an indispensable part of aluminum alloy, and the anodization technology is currently widely used.
The aluminum oxidation of the anode is oxidized, and the thin layer of alumina is formed on the surface, which has a thickness of 5 to 30 microns, and the hard anodized film can reach 25 to 150 microns. The anodized aluminum or alloys have improved its hardness and wear resistance, up to 250 to 500 kilograms per square millimeter, good heat resistance, hard anodized film melting point up to 2320K, excellent insulating, and resistant The wearing voltage is as high as 2000V, enhanced corrosion resistance.
The thin layer of the oxide film has a large amount of micropores, adsorbing various lubricants, suitable for manufacturing engine cylinders or other wear resistant parts; membrane microporous adsorption capacity is strongly colored into aesthetically beautiful color. Non-ferrous metals or alloys (such as aluminum, magnesium and their alloys, etc.) can be used for anodizing treatment, which is widely used in mechanical parts, aircraft automotive parts, precision instruments and radios, daily necessities and architectural decorations.