What is the difference between 201 stainless steel and 304 stainless steel?
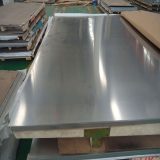
Gear steel should not only have good strength, toughness, wear resistance, withstand impact, bending and contact stress, but also have small deformation, high precision and low noise. In addition to the general quenching and tempering heat treatment, the production and processing technology of gears also adopts various surface hardening treatments such as carburizing and quenching, nitriding treatment, and high-frequency quenching. Generally, the technical requirements for gear steel in gear manufacturing are as follows:
(1) Sufficient core hardenability and good deep hardenability to ensure that no supercooled austenite decomposition products appear in the infiltrated layer and core during gear carburizing and quenching;
(2) The deformation of gears after carburizing and quenching is small, which eliminates or reduces grinding and reduces operating noise;
(3) Good formability;
(4) Good heat treatability.
High-quality gear steel is mainly manifested in three aspects: namely, the end hardenability band is narrow, the dispersion is small; the purity is high; the grains are fine and uniform. In addition, good processability (including cold, hot workability and free machinability) is also an important indicator of concern to the gear industry.
Replacing the previous mechanical property test with end hardenability is a major advance in evaluating the quality of gear steel. The stability of the end hardenability has a great influence on the deformation of the gear after heat treatment. The narrower the width of the hardenability band, the smaller the dispersion, the more conducive to the processing of the gear and the improvement of its meshing accuracy. my country's current GB/T5216-2004 "hardenability-preserving structural steel" standard in the hardenability belt "bandwidth" level and the United States, Germany's H steel (HH steel, HL steel) standard level is basically equivalent. At present, the bandwidth control of gears in my country is as follows: backbone enterprises are two-point control, J9 is generally 6-8HRC, and J15 is generally 6-10HRC; general enterprises require compliance with GB/T3077-1999 or single-point control. In foreign countries, the control of gear steel hardening bandwidth is generally controlled at 4-7HRC for the whole belt.
The influence of oxygen content on gear fatigue life has attracted more and more attention. Japan has done experiments on the relationship between the oxygen content and fatigue life of Cr, Cr-Mo, Cr-Ni-Mo carburized alloy steels. When the oxygen content drops from 25×10E-6 to below 10×10E-6 , and its fatigue life can be increased several times. China has also conducted comparative experiments on degassing and non-degassing of imported steels such as SCM420H and 20MnCr5, and it has been confirmed that the degassing is more than 50%. Due to the advanced technical equipment and process technology in industrialized countries, the oxygen content of gear steel is generally low. Since 1986, the oxygen content of gear steel imported from Japan, Germany, Austria and other countries has fluctuated in (7) ~18) x 10E-6. The oxygen content of 20CrMnTi produced by electric furnace single-smelting in China is about (30-40)×10E-6, and the oxygen content of gear steel produced by electric furnace + LF furnace double-smelting method is about 25×10E-6, which can reach 20×10E after VD vacuum treatment. -6 or less. In order to meet the new requirements of gear steel, the steel mills have undergone technological transformation, and the purity of the gear steel produced has also reached a high level, which has greatly shortened the gap with the international level.
At present, the gear industry standard has stipulated that the oxygen content of gear steel for automobiles is ≤20×10E-6, and many special steel manufacturers that use LF+VD or LF+RH refining treatment can control the oxygen content of gear steel to 15 ×10E-6 or less. Type B and D inclusions in non-metallic inclusions have a great influence on the fatigue life of gears. These two types of inclusions are also related to the oxygen content and have a great relationship with the size and distribution of non-metallic inclusions. At present, it is required that the B-type inclusions are not greater than 2, and the D-type inclusions are not greater than 1. Type A inclusions have little effect on the fatigue life of gear steel, and with the development of free-cutting gears, the upper and lower limits of sulfur content in steel are required. Request. Type C inclusions are silicate inclusions. Due to changes in smelting equipment, most domestic special steel mills can now reach levels below level 1.
The grain size is another important index of gear steel. The fine and uniform austenite grain size is important for stabilizing the end hardenability of the steel, reducing the deformation of the gear after heat treatment, and improving the brittle fracture resistance of the carburized steel. significance. Because the coarse grains make the carbon concentration of the carburized layer relatively high, the brittleness increases, the bending strength decreases, and the tooth surface is easy to peel off. If there is mixed crystals, it is possible that the heat treatment deformation between the teeth is out of order and cannot be matched. Grain refinement is mainly achieved by adding a certain amount of grain refinement elements such as Al, Ti, Nb, etc.
Now the more consistent view is: control the Al content to 0.020% to 0.055%, and at the same time, with a certain nitrogen content of 0.010% to 0.018%, so that it can form AIN to act as a pinning effect, which can prevent grain growth.
With the automation of gear processing lines, in order to continuously improve production efficiency, many countries are studying the use of free-cutting gear steels. In French and German standards, there are many steel grades with a lower limit of sulfur, and the sulfur content is generally only 0.020% to 0.035%, instead of the original concept that the lower the sulfur, the better. The sulfur content of these steels is much lower than that of my country's national standard GB731-88 free-cutting structural steel technical conditions (the lowest S=0.040% to 0.080%, the highest S=0.23% to 0.33%). Obviously, it is still difficult to improve the machinability only by conventional smelting methods, and it is necessary to improve the shape and distribution of sulfides through a suitable smelting process. In addition, air cooling treatment after forging and rolling of steel can prevent the appearance of granular bainite and improve the metallographic structure, which is also an effective way to improve the cutting performance.
During the solidification process of the steel, due to the effect of segregation and crystallization, the inhomogeneity of the composition will be caused in the horizontal and vertical directions of the solidification of the billet. The layered distribution is the band-like structure. The severe band-like structure not only increases the deformation after heat treatment of the gear, but also causes differences in the microhardness of each part of the tooth height after the carburizing treatment of the gear, which affects the fatigue life of the gear.
Different steel grades have different severity levels of banded structures. The banded structures of Cr-Mo and Cr-Ni-Mo steels are more serious than other steels. Because the band structure is not easy to eliminate, gear factories generally require the band structure to be less than grade 3. Because the equiaxed crystal area of the die casting material is larger than that of the continuous casting material, the uniformity of its composition is better than that of the continuous casting material, and the band structure is lighter. As long as the pouring temperature and speed are well controlled, most of the heat numbers can meet the requirements of less than grade 3. . It is relatively difficult for continuous castings to meet this requirement. The fundamental solution to the band-like structure is to reduce the segregation of components, combined with the appropriate cooling rate after rolling.
Gear steels are all steels used for hot upsetting, and the surface quality of the steels is very strict. Whether it is GB/T3077-1999 or the "Technical Conditions for Gear Steels for Vehicles" recently formulated by the China Gear Association strict requirements. Compared with the advanced level of foreign countries, there is still a big gap between the current surface quality of gear steel in my country.
Because Si is most likely to cause internal oxidation in the carburized layer to form a "black network structure" defect, which reduces the fatigue life sharply. Therefore, the carburizing gear steel tends to reduce the [Si] content in the steel (Si≤0.12%), and it also speeds up the carburizing speed of the gear. Ti forms a sharp, angular and very hard Ti(C, N) compound with N and C in steel, which does not deform during rolling and causes cracks between it and the matrix. Therefore, it has a great influence on the fatigue life of the gear, so it is not suitable to add more Ti to refine the grains or prevent mixed crystals in the gear steel. It is recommended to use A1 or add a small amount of Nb to refine the grains.