What is the difference between 201 stainless steel and 304 stainless steel?
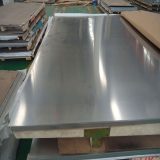
Moenl K500 is a precipitation hardening nickel-copper aluminum alloy that combines the excellent corrosion resistance of Moenl400 alloy with higher strength and hardness, outperforming other nickel-copper alloys. The addition of titanium and aluminum makes K500 twice the tensile strength of the 400 alloy and three times the yield strength of the 400 alloy. This high strength can be maintained all the way down to 649°C, while the material remains ductile and ductile at temperatures as low as -240°C. Another advantage of K500 alloy is that it maintains non-magnetic properties at temperatures as low as -129°C. Therefore, K500 is an ideal material for applications with or containing electronics where the magnetic field is a disturbing factor, such as downhole equipment. K500 also has spark resistance and excellent corrosion resistance, resistant to many chemical elements and marine environments such as salts, alkalis, acids, non-oxidizing acids.
Annealing treatment can be used to soften the metal matrix after processing, and can also be used to dissolve the age-hardening phase. Although the low temperature range of 760℃-871℃ can also obtain sufficient softening effect, in order to achieve the best effect of subsequent aging hardening, it is recommended to use 982℃ for the annealing temperature of hot-worked products and 1038℃ for cold-drawn products.
When the temperature exceeds 982 °C, the grain growth rate is quite fast. If a fine grain structure is required, the high temperature heat treatment time needs to be controlled to the shortest.In order to obtain the best aging reaction and maximum softening results, an effective water quenching treatment is required immediately after heat treatment. Failure to perform water quenching immediately or the quenching speed is very slow will result in the precipitation of part of the age-hardening phase, which will impair the aging reaction. Adding 2% (by volume) alcohol to the water quenching liquid can reduce oxidation and facilitate pickling.
Hold at 594℃-607℃ for 6 hours, then carry out furnace cooling, and reduce the temperature to 482℃ at the rate of -9.5℃~-3.9℃/hour. From 482°C to room temperature, furnace cooling or air cooling can be used, and there is no need to control the cooling rate. This process is suitable for as-forged, quenched and annealed forged, annealed, hot-rolled rods, large-diameter cold-drawn bars (>38mm in diameter) and softened and tempered wire and strip.
Hold at 593°C-607°C for 8 hours or longer, then cool to 482°C with a cooling rate not exceeding -9.5°C~ -3.9°C/hour. Higher hardness can be achieved if the material has undergone only a small amount of cold work, holding for up to 16 hours. Generally speaking, the holding time of materials with initial hardness of 175-200HB needs 16 hours. The material close to 250HB (25Rc) can fully reach the hardness after 8 hours of heat preservation. The process is suitable for cold drawn rods, rods, strip in semi-rigid state and cold heading materials.
Hold at 527℃-538℃ for 6 hours, then cool to 482℃, the cooling rate does not exceed -9.5℃~-3.9℃/hour. If the initial hardness of the material is close to the lower hardness limit, higher hardness can be obtained by holding for 8-10 hours. The process is suitable for elastically tempered strip, spring wire and heavily cold-worked workpieces such as cold-formed beads.
Note: Cooling can be carried out in steps at 37.7°C, and each step is kept for 4-6 hours. For example, the heat treatment process of Process 1 is 593°C for 16 hours + 593°C for 4-6 hours + 482°C for 4-6 hours. However, heat treatment according to the above-mentioned process flow of 1.2.3 usually obtains materials with higher performance.
In some cases, the heat treatment time needs to be shortened, in order to reduce costs or to obtain some intermediate properties. It is difficult to determine the specific heat treatment time one by one. It is recommended to put test pieces according to the cross-sectional specifications of the material to explore the heat treatment time.
Excessive artificial aging reduces material properties, and subsequent aging treatments can no longer improve material properties. To strengthen over artificially aged materials, solution treatment (982-1037°C) must be performed to re-dissolve the age-hardened components and then re-age Treatment. The benefits of cold working are offset by the annealing treatment. The highest strength a material can achieve is related to the annealed and aged condition.
Age-hardened materials can achieve maximum hardness, but reheat treatment does not improve material properties. If the cooling rate of the first heat treatment is rapid, between 565-426 °C, reheat treatment may slightly improve the material properties. If the hardened The material is heat-treated at a temperature above 593°C, and then cooled, and the material properties will decrease. The hardened K500 needs to be continuously heated at 426°C for a long time. The aging effect will slowly appear in the first month, and it will not be heated afterward. There are big changes.
The annealed, hot worked and quenched condition of Monel K500 are more suitable for heavy machining. Age hardened material can be finished to near precision and then finished again. The recommended process steps are machining to oversize, age hardening, and trimming to size. Aging produces a little permanent shrinkage of the material (approximately 0.0002in/in).
(1) Chemical processing industry
(2) Maritime engineering
(3) Oil and gas exploitation
(1) Centrifugal pump
(2) Parts of oil and gas extraction equipment
(3) Transmission shaft
(4) Pump shaft
(5) Spring
(6) Valves and valve parts