What is the difference between 201 stainless steel and 304 stainless steel?
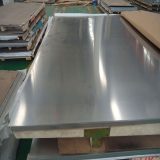
Steel parts can improve its strength, hardness and abrasion resistance after quenching, but the original size or shape of the workpiece will change when people do not want during quenching. This change will become a defect that affects the quality of the product. First of all, we need to know what defects will occur in quenching, what are the causes, and find the corresponding solution. The quenching quality defects and control are explained from the following aspects.
The type of quenching distortion can be divided into two categories, that is, volume distortion and shape distortion.
Various organizations before and after quenching are the main reasons for the volume change. The volume of the ratio of Matthery → Belene → Pearl Light → Austenite decreases in order. The original tissue is the workpiece of the pearl glory to the martial arts, and the volume is swollen. If there is a large number of residues in Octobic, the volume may be reduced. Only the workpiece with a particularly high accuracy will consider the volume of uniform swelling and cause changes in volume.
The relative position or size of the workpiece changes, such as the curved of the rods, the inner pores and shrinkage, and the change of the pitch of the pores. There are the following reasons for the formation of distortion:
(1) Unemployment of heating temperature, the thermal stress formed causes distortion or the workpiece is unreasonable in the furnace, and often causes creep distortion at high temperature due to self -weight.
(2) During heating, as the heating temperature increases, the yield strength of the steel decreases, and the residual stress (cold deformation stress, welding stress, machine processing stress, etc.) within the workpiece reaches the yield strength at high temperature, which will cause the workpiece to cause the workpiece Uniform plasticity deformation causes shape distortion and residual stress relaxation.
(3) The thermal stress and tissue stress of the different time formation during quenching and cooling cause the workpiece to deform local plasticity. The complicated workpiece, due to the particularity of its structure, during quenching, the speed during heat and cooling is different, which increases its deformation tendency.
(1) Adopting a reasonable heat treatment process can effectively reduce distortion. If the quenching heating temperature is reduced; slowly heating or preheating of the workpiece; static heating method, extremely slender and extremely thin workpieces, in order to reduce the impact of the mixing of salt bath on the workpiece, the power -off heating can be used; the section size is smaller. If the intensity of the heart is not high, it is not highly heated; reasonably bundles and hangs the workpiece; a reasonable quenching method is adopted according to the shape of the work; Before quenching, the workpiece deforms from reverse, causing it to offset the distortion after quenching.
(2) Reasonable design parts. For example, the shape of the workpiece strives to be symmetrical to avoid the difference in the cross section, thereby reducing the distortion caused by uneven cooling; in order to reduce the expansion or narrowing of the slot swelling, it will make it a closed structure before quenching. Add muscles at the groove and cut it out after quenching; set the process holes to reduce the reduction of cavity; the complex parts adopts a combined structure, and a complex workpiece will be decomposed into several simple parts. Select steel, such as high accuracy, allowing work molds with less heat treatment distortion, micro -distortion steel can be selected, and pre -hard steel can also be used for high -precision plastic molds.
(3) Reasonable forging and preparing heat treatment. Severe carbide bias and band tissue make the quenching distortion of the opposite sex or irregularity. By forging the distribution of carbides, it can not only reduce distortion, but also improve the service life of the workpiece.
For the distortion of parts after heat treatment, cold pressure schools can be used, hot schools, straight schools, direct schools, recovery schools straight, counterattack school straight, shrinkage treatment and other methods.
Cold pressure school is the highest point of the bending workpiece at the highest point of the protruding workpiece, so that plastic deformation occurs. This method is suitable for axis workpiece with hardness of less than 35HRC; the hot school is to heat up the convex part with oxylay acetylene flames, and then Use water or oil to cool quickly to shrink the heating part under thermal stress. This method is suitable for workpieces with hardness greater than 35-40HRC; while thermal school is the workpiece is quenching to the nearby temperature of the MS. The phase transformer is super plastic, so that the distortion is corrected; the recovery school is exerting the workpiece to the external force, and then the ignition temperature is higher than 300 ° C; Plastic deformation; shrinking hole treatment is to heat up to 600-700 ° C after quenching and swelling. In order to prevent water in the pores, two pieces of sheets are used to cover the ends of the workpiece. The hole shrinks, and after multiple or repeated operations, the swelling hole can be corrected.
The quenching cracking is the cracking phenomenon caused by the fracture intensity of the material exceeding the material. The cracks are discontinuously distributed, and there are traces of quenching oil or saline, anaerobic dioxide, and no decarburized phenomenon on both sides of the crack. There are several points and reasons for the occurrence of quenching cracks:
(1) Material management is chaotic, and high -carbon steel or high -carbon alloy steel is used as low, medium -carbon steel, and uses water quenching.
(2) Improper cooling. Fast cold below the MS temperature caused a cracking due to the great stress of the tissue. Such as the water-oil dual medium quenching, stay in the water for a long time, and the quenching oil contains too much water.
(3) When the hardness of the non -quenching workpiece is 36 to 45HRC, the quenching cracks are formed at the junction of the hardened layer and the non -quenching layer. The hardness of the heart is less than 36HRC, and the hard force at the junction is reduced. The hardness of the heart is greater than 45HRC, which shows that there are already martyl tissues.
(4) The workpiece with the most dangerous quenching size is easy to form a quenching crack. There is a dangerous quenching size when all the workpieces are quenched. The diameter is: 8-15mm during water quenching; 25-40mm during oil quenching. When the size is smaller than the most dangerous quenching size, the temperature difference between the heart and the surface is small, the hardening force is small, and it is not easy to crack. On the contrary, it increases.
(5) Severe surface decarburization is easy to form mesh cracks. The decarburization layer martensite is smaller than the volume, and is stabilized by tensile stress, which is easy to form mesh -like cracks.
(6) Deep holes with smaller inner diameter. The inner surface cooling is much smaller than the outer surface, and the residual thermal stress effect is small.
(7) The heating temperature of quenching is too high, causing grains to be rough, weakened in the crystal world, reduced the crispness of steel, and the quenching is easy to crack.
(8) Repeatedly excessive annealing before quenching, a large tendency of overheating, the quenching stress of the previous paragraph fails to completely eliminate, and the surface decarbon caused by multiple heating will promote quenching and cracking.
(9) The large -section high -alloy steel workpiece is not preheated or heated too fast when heating, and the thermal stress or tissue stress during heating increases, causing cracking.
(10) Primitive tissue is poor, such as high -carbon steel balloization of the quality of heating, its tissue is a sheet or dot -shaped pearl light, with a large tendency of heat; the grain is rough, the martensite content is high, and the quenching and cracking tendency is large.
(11) The raw materials are slightly cracking, non -metal mixed objects, and severe carbonized bias analysis of quenching and cracking tendency to increase. For example, non -metal and debris or severe carbides are announced in the direction of rolling. Due to the opposite sex of each orientation of mechanical properties, its horizontal performance is 30%to 50%lower than the vertical performance. The distribution direction of metal miscellaneous or carbides is vertically cracking.
(12) Forging cracks expand during quenching. When the quenching and heating in the furnace, there are black oxidative skin on the broken broken surface, and there is a decarburized layer on both sides of the crack.
(13) Cracking. The cracks are mostly mesh, and the crystal boundary is aerobic and melting.
(14) Steel with low quenchability, when clamping quenching with pliers, the clamping site is quenched and cold. Large, easy to crack.
(15) High -speed steel and high -chromium steel grading quench, the workpiece is not cold to room temperature, and is rushing to clean (because fast cold below MS) causes cracking.
(16) The thermal stress and tissue stress formed by deep -cold treatment are relatively large, and the crisp strength of low -temperature materials is low, which is easy to produce quenching and cracking.
(17) Failure to rectify after quenching, and the micro -cracks inside the workpiece expand under the action of quenching stress to form a macro crack.
(1) Improve workpiece structure. The cross -section strives to be uniform. There should be a rounded transition at different sections to minimize the non -pores and sharp corners to avoid cracking caused by stress concentration.
(2) Reasonable selection of steel. The complex and cracking workpieces should be made to make high -quenching alloy steel in order to use a slow and slow quenching medium to reduce quenching stress.
(3) The raw materials should avoid micro -cracks and severe non -metal mixed objects and carbides.
(4) Pre -heat treatment is carried out correctly to avoid defects of positive fire and annealing tissue.
(5) Select the heating parameters correctly.
(6) Reasonably select the quenching medium and quenching method.
(7) Local bandaging parts of the workpiece, such as sharp corners, thin walls, holes, etc.
(8) After quenching the cracking workpiece, it should be recovered or returned in time after quenching.