What is the difference between 201 stainless steel and 304 stainless steel?
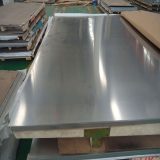
A superalloy, or high-performance alloy, is an alloy with the ability to operate at a high fraction of its melting point.The crystal structure is typically face-centered cubic (FCC) austenitic. Examples of such alloys are Hastelloy, Inconel, Waspaloy, Rene alloys, Incoloy, MP98T, TMS alloys, and CMSX single crystal alloys.
Superalloy development has relied heavily on both chemical and process innovations. Superalloys develop high temperature strength through solid solution strengthening and precipitation strengthening from secondary phase precipitates such as gamma prime and carbides. Oxidation or corrosion resistance is provided by elements such as aluminium and chromium. Superalloys are often cast as a single crystal—while grain boundaries may provide strength at low temperatures, they decrease creep resistance.
Superalloys are mainly used in the manufacture of important parts of gas turbine engines, such as turbine blades, turbine disks, bearing rings, flame tube mounts, etc. Such parts not only require high high temperature performance and good fatigue performance, but also require oxidation resistance, corrosion resistance and certain plasticity.
The forging characteristics of superalloy forgings are:
Due to the high degree of alloying, the superalloy has the heterogeneity of the structure and the complex phase composition, so the process plasticity is low. Especially at high temperature, when impurity elements such as s, Pb, and Sn are contained, the bonding force between grains is often weakened and the plasticity is reduced.
Superalloys generally use the total content of strengthening elements aluminum and titanium to judge the level of plasticity. When the total content is greater than or equal to 6% (the most qualitative fraction), the plasticity will be very low. The process plasticity of nickel-based superalloys is lower than that of iron-based superalloys. The process plasticity of superalloys is sensitive to deformation rate and stress state. Some alloy ingots and intermediate billets require low-speed deformation and wrapping upsetting, wrapping rolling, and even wrapping extrusion before they can be formed.
Due to the complex composition of the superalloy, the recrystallization temperature is high, the recrystallization speed is slow, and it has a high deformation resistance and hardening tendency at the deformation temperature. The deformation resistance is generally 4 to 7 times that of ordinary structural steel.
Compared with carbon steel, superalloy has a low melting point, and if the heating temperature is too high, it is easy to cause overheating and overburning. If the stop forging temperature is too low, the plasticity is low, the deformation resistance is large, and the mixed deformation of cold and heat is easy to occur, resulting in uneven coarse grains of the forgings. Therefore, the forging temperature range of superalloys is very narrow, generally only about 200 °C. The forging temperature range of nickel-based heat-resistant alloys is narrower, most of which are between 100 and 150 °C, and some are even less than 100 °C.
The thermal conductivity of superalloys at low temperature is much lower than that of carbon steel, so generally, slow preheating is required in the range of 700~800 °C, otherwise it will cause a large temperature ton force and make the heating metal in a brittle state.
Aluminum alloys can be heated before forging by various heating equipment, such as resistance furnace, gas furnace, oil furnace, induction heating device, fluid particle furnace, etc. Generally, a resistance furnace is used for heating. In this case, the furnace should be equipped with a furnace gas device to make the furnace temperature uniform.
When using gas or oil furnaces, low fuel must be used, and the flames in the furnace are not allowed to directly touch the surface of the billet. Foreign countries believe that the muffle furnace is the best for aluminum alloy forging heating, and the gas-fired semi-closed furnace has been widely used.
When the aluminum alloy forging process is automated, the commonly used heating methods include induction heating, resistance heating and fluid particle heating.
The forging temperature range of aluminum alloy is narrow, and it is easy to overheat and overheat, so it is necessary to accurately measure and control the temperature, and the furnace temperature deviation is preferably within the range of ±5 °C.
Aluminum alloy has good thermal conductivity, so the thickness of the blank can be directly heated into the high-temperature furnace without preheating, but the heating time is longer than that of ordinary carbon steel, because the aluminum alloy must be dissolved when it is heated, so as to make the alloy Uniform organization, plastic X.
The heating time of the aluminum alloy billet is calculated as 1.5 to 2 minutes per millimeter of diameter or thickness. The dissolution process of the chemical phase is related to the size, shape, distribution characteristics and its own X quality of the chemical phase. The coarser the structure, the slower the dissolution. Therefore, the upper limit of the heating time should be taken for ingots, large forgings and rough bars (φ1oomm).
For billets with high alloying element content, the heating time is longer. For example, LC 4 should have a longer heating time than LD2 alloy. Under normal circumstances, the heating time of aluminum alloy is 1-2 hours. If it is a last resort, the heating time can exceed 4-6 hours. If it is longer, it is recommended to take the metal out of the furnace to overheat and absorb.