What is the difference between 201 stainless steel and 304 stainless steel?
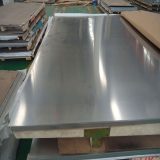
Inconel 625 alloy was developed in the 1950s to meet the needs of high-strength main steam piping materials. A patent application for this alloy was filed on January 24, 196, and patent #3,160,500 was granted to H.L. EiseIstein and J. Gadbut on December 8, 1964.Subsequently, 625Plus, Inconel725 were derived from the 625 alloy, Iconel718 was developed, and Inconel706, PWA 1472 and Rene220 were derived from the 718 alloy.
Alloy 625 is a non-magnetic alloy with good strength and toughness from freezing temperature to 2000°F, it has excellent fatigue strength and resistance to chloride ion stress corrosion cracking. Some of its typical uses are as thermal insulation, metal components in chemical plants and special seawater applications.
Alloy 625 is a nickel-iron-based austenite containing a large amount of chromium (20-25wt%), aluminum (8-10wt%), iron (5wt%), and niobium (3.5-4.5wt%) as the main additive element Deformed alloys. Due to its special combination of mechanical properties, processability and corrosion resistance, this superalloy has been widely used; it is one of the alloys with the best corrosion resistance in various media and industrial atmospheres. Alloy 625 is generally not considered an age hardening superalloy due to its low Al and Ti content. Then, since it contains Fe and Nb (+Ta), metastable ordered Y” phase (tetragonal DO22) and δ phase (orthorhombic DO2) occur during long-term aging of solution-treated 625 alloy )precipitation. Although Y” and δ phases both have the matrix composition of Ni3Nb, but there are different stacking orders on the atomically dense planes, on these planes Ni and Nb atoms have different atomic arrangements, so the mechanical properties of the 625 alloy are mainly It is caused by solid solution hardening and strain hardening caused by Mo, so it is usually not used at temperatures above 625 degrees.
Ni | Cr | Mo | Fe | Nb + Ta | Co | Mn | Al |
---|---|---|---|---|---|---|---|
58 - 71% | 21 - 23% | 8 - 10 % | 5 % | 3.2 - 3.8 % | 1 % max. | 0.5% max. | 0.4% max. |
The strength of Inconel 625 lies not only in its nickel-chromium base but also the hardening mechanism of niobium and molybdenum. The alloy matrix is strengthened by the interaction of niobium with molybdenum that offers high strength without the need for precipitation-hardening treatment. The tensile strength of this superalloy is 690 MPa, while its yield strength measures 275 MPa.
With a melting point of about 1300°C and a thermal expansion coefficient of 1.28 x 10-5 1/K (at 20°C), Inconel 625 resists a wide range of temperature extremes from cryogenic to extremely high.
At high temperatures in the presence of oxidising agents, the titanium and niobium compositions of the oxide film on Inconel 625 increase drastically to form a natural protective layer in the material.
The unique combination of its components makes Inconel 625 highly resistant to corrosive substances. This is the reason why this superalloy works excellently under high saline seawater, and more so in milder environments such as fresh water and standard atmospheric conditions.
Upon exposure to oxidising agents, Inconel 625 is protected naturally by its nickel-chromium matrix. Meanwhile, molybdenum protects the material against pitting corrosion. In 15% sulfuric acid, the material corrodes at a minimal rate of 0.188 mm per year.
Inconel 625 was designed to have better weldability than earlier alloys, with no signs of cracking when exposed to strain and temperature changes post-welding. Its high creep resistance and yield strength make this superalloy a good choice for tubes, piping, and plant equipment that require welding.
1)Excellent mechanical properties at very low and very high temperatures.
2)Excellent resistance to pitting, crevice and intergranular corrosion.
3)Chloride-induced stress corrosion cracking is almost completely absent.
4)High oxidation resistance at high temperatures up to 1050C.
5)Good resistance to acids (such as nitric, phosphoric, sulfuric and hydrochloric) as well as bases makes it possible to build thin structural components with high heat transfer properties.
Owing to its high corrosion resistance-- especially pitting and crevice resistance, Inconel 625 is an ideal for high saline, underwater applications. The material is used as propeller blades for boats, mooring lines to secure ships and similar vessels, accessories and fixtures for submarines, and parts for oceanographic equipment.
The superalloy has also found its way into the aircraft industry, particularly for exhaust equipment, fuel lines, heat exchanger casings, and rocket components. This is because Inconel 625 works well even in extreme temperatures under high stress.
Its strength as well as its resistance to corrosion and stress make Inconel 625 a suitable component of nuclear reactors, particularly in the control rod and reactor core. Nuclear systems also generally involve high temperatures beyond 650°C, in which the strength of Inconel 625 can withstand.
Because the alloy is conveniently fabricable and resistant to heat and corrosion, it is a useful ingredient in the production of manufacturing equipment such as vessels, heat exchangers, valves, and fluid distribution systems. Its excellent weldability also makes it a suitable component for pipes and tubes used in manufacturing plants.