What is the difference between 201 stainless steel and 304 stainless steel?
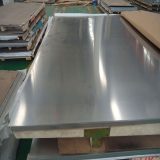
C10100 OXYGEN-FREE COPPER is produced by the direct conversion of selected refined cathodes under carefully controlled conditions to prevent any contamination of the pure oxygen-free metal during processing. The method of producing O.F.H.C. Copper ensures extra high grade of metal with a copper content of 99.99%. With such a small content of extraneous elements, the inherent properties of elemental copper are brought forth to a high degree. Characteristics are high ductility, high electrical and thermal conductivity, high impact strength, good creep resistance, ease of welding, and low volatility under high vacuum. C10100 Copper Conforms to ASTM B187 round bar and ASTM B152 for plate.
C14500 TELLURIUM COPPER is adapted for use in high-speed automatic screw machines. The copper tellurium precipitations become finely dispersed throughout the matrix and result in small chips enabling a much higher machining speed than with pure copper. C14500 tellurium copper has a machinability rating scale of 85%, compared to pure copper of 20%, ensuring longer tool life. Resistance to hydrogen embrittlement combined with its' high electrical and thermal conductivity make it the ideal choice for electrical applications requiring extensive machining and corrosion resistance. Conforms to specification ASTM B301 , SAE J461, J463, B-124.
C18150 CHROMIUM ZIRCONIUM COPPER (RWMA CLASS 2) has improved creep resistance at high operating temperatures from the addition of zirconium to chromium copper. Chromium-Zirconium Copper reduces sticking and deformation of electrodes to the work surface during spot welding of galvanized/coated materials. C18150 specifically is for cap style resistance welding electrodes and weld wheels. C18150 Chromium-Zirconium Copper conforms to specifications SAE J461,463;RWMA Class 2, ISO5182-1991.
C18200 CHROMIUM COPPER (RWMA CLASS 2) is a heat treatable, corrosion resistant alloy which combines high electrical conductivity with high strength. Class 2 chrome copper is a superior resistance welding electrode material specifically recommended for high-level production spot welding and seam welding of clean mild steels, low alloy steels, low conductivity brasses, and bronzes. Typical applications include projection welding dies, seam welder shafts and bearings, flash and butt welding dies, resistance welding electrodes, spot welding tips, seam welding wheels, electrode holder jaws, cable connectors, current carrying structural members, electrical switch gears and electrical and thermal conductors requiring greater strength than copper.
C17510 BERYLLIUM COPPER (RWMA CLASS 3) has high thermal conductivity combined with good hardness and high-temperature strength. This alloy is being chosen with increasing frequency for applications requiring a combination of high electrical conductivity and mechanical strength, and for applications requiring wear and corrosion resistance. Alloy C17510 Class III beryllium copper is specifically recommended for projection welding dies, flash and butt welding dies, current carrying shafts and bushings. Class III alloy (having higher strength than class II), is recommended for highly stressed welder structural current carrying members and heavy-duty offset electrode holders. Class III alloy is generally recommended for spot welding and seam welding wheels having high electrical resistance, such as stainless steels. C17510 Beryllium Copper conforms to specifications ASTM B441 (ROD), ASTM B534 (PLATE) , RWMA Class III.
C36000 FREE-MACHINING BRASS is ideally suited for high-speed machining operations with its superior machinability, thread rolling and knurling characteristics. Its machinability rating of 100 is standard against which all other copper alloys are rated. It is easily soldered or brazed and has good resistance to corrosion. Typical applications included gears, pinions, plumbing ware fittings, adapters, valves, valve stems and screw machine products. Conforms to specification ASTM B16, SAE J461, AMS 4610.
C46400 NAVAL BRASS provides a high degree of corrosion resistance to seawater at even higher than normal temperatures while also assuring greater strength and rigidity. It possesses an excellent capacity for hot working and adapts well to hot forging and pressing. This naval brass also lends itself to drawing, forming, bending and heading. It is readily soldered, brazed and welded. Typical applications include nuts, bolts, rivets, valve stems, pump shafts and marine hardware. Conforms to specification ASTM B21, SAE J461, AMS 4611, 4612, FEDERAL QQ-B-639, SAE J463.
C51000 PHOSPHOR BRONZE possesses a higher yield strength than is readily available in most cast products. C51000 combines strength, toughness and good ductility with excellent resistance to fatigue. Typical applications for phosphor bronze include bearings, bushings, gears, pinions, shafts, thrust washers and valve parts. Can be readily brazed or soldered. Capacity for being cold worked is good. Conforms to specifications ASTM B139, QQ-B750, SAE J461, ASME SB171.
C54400 PHOSPHOR BRONZE is an excellent wrought material for use in the manufacture of bearings. C54400 Phosphor Bronze is also free cutting due to its nominal 3.5% lead content. When annealed, the metal can be bent, formed, blanked and stamped. Like other phosphor bronze alloys, it is known for its toughness, strength, low coefficient of friction and fine grain. The alloy is also resistant to fatigue, wear, and chemical corrosion. C54400 Phosphor Bronze conforms to specification ASTM B139.
C61400 ALUMINUM BRONZE has a high tensile strength and a good yield along with an inherent toughness and ductility not usually found in a single alpha phase aluminum bronze. During the extrusion process for bar or in the rolling process for plate, the metal is hot worked resulting in a compact grain structure free of inclusions or other defects resulting in improved physical properties. C61400 Aluminum Bronze is used whenever good resistance to corrosion, erosion, abrasion, and cavitation-pitting is crucial. C61400 Aluminum Bronze conforms to specifications SAE J461, ASTM B169, FEDERAL QQ-C-450, SAE J463, ASME SB169, ASME SB171, ASTM B169 and ASTM B171.
C63000 NICKEL ALUMINUM BRONZE is an excellent choice for applications involving heavy loads, adhesive wear, friction, abrasive wear, and corrosion. The addition of nickel increases the alloys strength without diminishing its excellent ductility, toughness and corrosion resistance. Alloy C63000 nickel aluminum bronze has gained wide acceptance in the aircraft industry for severe landing gear service in products such as strut bearings, main pistons, trunnion bearings and similar vital components. C63000 Nickel Aluminum Bronze conforms to specifications ASTM B150, AMS 4640, SAE J463, QQ-C-465B, ASME SB150, ASTM B-150, B-124, B-171, B-283, ASME SB171, ASTM B171, QQ-C-450 A.
C64200 SILICON ALUMINUM BRONZE is a non-magnetic alloy that has good fatigue strength and galling resistance. The addition of silicon to this aluminum bronze alloy gives it the highest machinability rating of bronzes and brasses without the addition of lead. Copper alloy C64200 has combined strength, corrosion and wear resistance and is a good choice for parts that require extensive machining. C64200 silicon aluminum bronze conforms to ASTM B150, ASTM B249, QQ-C-465, AMS 4634, SAE J461, SAE J463.
C67300 SILICON MANGANESE BRONZE is a high strength leaded silicon manganese bronze with good bearing qualities. This alloy maintains high impact resistance with excellent machinability making it well suited for clutch bearings, shaft bushings, sleeve bearings, thrust bearings, pump parts, drive shafts, bearing pins, wear plates, gears and cams. Resists squashing out under high loads and extreme wear applications. C67300 Manganese Bronze conforms to specifications SAE J461, SAE J463.
C67500 MANGANESE BRONZE is a high strength leaded manganese bronze alloy that is strong, rigid and abrasion resistant. It is also an excellent brazing alloy. Often used in automotive and hardware manufacturing, this product is used in bushings, clutch disks, pump rods, shafting, balls, valve stems, and bodies. C67500 possess hot working properties and can be die forged into valves, connectors and other components for military applications. C67500 Manganese Bronze conforms to specifications ASTM B138, QQ-B-728, SAE J461, SAE J463.
C70600 (90/10) COPPER NICKEL offers excellent corrosion resistance to brine water, organic compounds, salts and diluted non-oxidizing acids. This alloy is especially resistant to marine saltwater environments. C70600 copper nickel has additions of iron and manganese which is necessary to maintain good corrosion resistance. This alloy is especially suited for condenser plates, salt water pipe fittings, salt water piping systems, flanges and propeller sleeves. C70600 Copper Nickel conforms to specifications ASTM B171, ASME SB171, MIL-C-1726F, MIL-C-24679.
C71500 (70/30) COPPER NICKEL has all the characteristics of C70600 (90/10) copper-nickel, but offers better corrosion resistance in high-velocity seawater. The operating temperature for C71500 (70/30) is also much higher than that of C70600 (90/10), which can assure a long and reliable service life for parts in these conditions. C71500 with its higher nickel content offers added corrosion resistance for critical marine hardware. C71500 Copper Nickel alloy conforms to specifications ASTM B171, ASME SB171, MIL-C-1726F, MIL-C-24679.