What is the difference between 201 stainless steel and 304 stainless steel?
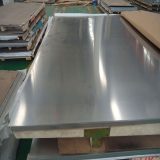
The casting is a metal molded article obtained by various casting methods, i.e., a liquid metal that is smelted, injects a pre-prepared molding method with pouring, irradiation, inhalation or other casting method, and then drying after being worn. The resulting object having a shape, size, and performance.
Modern machinery manufacturing has no variety of copper castings. We have made a brief introduction to the selection of the division surface (sand box contact surface). details as follows:
1)Use as few partial surfaces as possible.
2)Try to reduce the number of cores and activity blocks.
3)Try to place all or most of the copper castings in the same sandbox to prevent defects such as mimic, fly, burrs, and ensure the accuracy of the size of the casting.
4)The work surface and processing of the castings should be in the same sandbox. If there are many machined surfaces of the castings, and it is impossible to place all in the same side of the partial surface, the processing reference plane and most of the machining surfaces should be placed on the same side of the respective surface.
5)Try to choose a plane to avoid surface layouts, try to select a large section simplified mold manufacturing and styling process.
6)In order to facilitate molding, lower core, unpacking, inspection and test, try to place the cavity in the lower box.
The above is the principle of selection in the casting process. For parts that are complicated in shape, it is difficult to processed by CNC machine tools, which is more economical. Copper castings have sufficient corrosion resistance and wear resistance to meet the needs of general machining.
Copper casting production is uninterrupted. In order to ensure the normal operation of the equipment, the support of copper castings is required. From its advantages, we can see which processes have been used in production and processing? The following is a detailed description of the copper casting process:
1)During the production of copper castings, the development and implementation of die-casting processes is closely related to mold quality, die-casting equipment, and operators' operation technology. Under existing die-casting equipment conditions, it is difficult to safely and reliably control the die-casting process parameters.
2)It is the process of completing the basic operation of the die-casting process using die-casting equipment, die-casting materials and molds. In the production process, if the process parameters and the main parameters are not strict, it will cause the aluminum alloy die casting, the incrementing, deformation, and fouling.
3)Copper alloy die casting is an indispensable part in the aluminum alloy die casting production. When describing die-casting modes, the overall layout of the mold and the layout of the mold parts should be made more reasonable, easy to make and use.
4)In order to prevent the mold in the die casting process, the metal fluid is stabilized in the mold, the casting is uniform, and the die-casting process is fully automated, and there is no defect. In addition, the appropriate mold information is reasonably selected according to the detailed production batch, the material conditions, and the like.
After the production of copper castings, further processing is needed to meet the production needs. According to different requirements, different processing processes are used, and different processes may have different effects in their applications.
In general, the surface of the copper casting is rough, there are many holes, and the copper surface is not clean, covered with sand, white wax and other substances. But if you don't clean up in advance, it is hard to get the silver. Therefore, after the surface of the clean copper casting, a layer of silver is applied to the surface of the precision copper casting, which is more qualified. Due to the characteristics of precision cast copper parts, the electroplating process is very strict, enabling the product to create a satisfactory product. However, it should be noted that in order to avoid the impact of the casting process, the residual solution in the gap between copper must be removed. If there is a residual material inside, it will affect the next casting. Copper castings are longer than we imagined. We must have patience. For a long time, the color balance of protecting the paint, sometimes casting is not a good thing, so quality often does not guarantee.
1) The copper casting can be made of a very complex cavity of the shape. Such as various cases, machine tools, cylinders, cylinder heads, and the like.
2) Technology flexible and wide adaptability. The size of the liquid molding is almost unlimited, and its weight can be from several hundred tons, the wall thickness can be dissolved from 0.5 mm to 1 meter, which can be dissolved into a liquid metal material for liquid forming. For non-cast iron, liquid forming is the only way to produce their blank or part.
3) Liquid formation is low. Liquid forming can directly utilize waste and chips, and the equipment cost is low. At the same time, the processing margins of liquid forming parts are small, and metal is saved.
Advantages of copper castings:
Copper is not strange, it is often used in our daily life. However, many copper made of small parts are not easy to find as part of the part. For example, we use door handles, lock cores, heat sinks, water pipes, water heaters, iron, etc., all of which are precision cast copper parts. In fact, the application of my country's precision cast copper parts can be said that it is thousands of years ago, ancient copper castings began to cast, modern sand casting is the most common application, accounting for 80% of the total castings. Colored metal castings such as aluminum, magnesium, zinc are mostly a die casting. In the field of mechanical, some precision castings can also be used directly as part of the machine.
Machine copper casting varieties, the most complicated shape, the maximum dosage, accounting for 60% of total castings. This is followed by the steel ingot mold and the pipeline for engineering. Copper casting mainly uses a blank of machine components, some precision castings, can also be used as part of the machine. Castings account for a large specific gravity in mechanical products, such as tractors, the weight of the casting accounts for about 50 to 70% of the weight of the machine, 40 ~ 70% of the agricultural machinery, 70-90% of the machine, internal combustion engine, etc.
Causes and solutions for copper casting air holes and bubbles:
Defect feature: The pneumatic hole in the three-casting wall is generally circular or elliptical, with a smooth surface, which is generally a bright oxide, sometimes oil yellow. Surface air holes, bubbles can be found by sandblasting, and internal pore bubbles can be found in black air bubbles on the X-plasheet by X-light vertical or mechanical machining.
cause:
1)Pouring alloy is not smooth, involved in gas
2)Mixed organic impurities (such as dried coaches, grassroots horses, etc.)
3)Casting and skin core
4)Cold iron surface has a shrinkage hole
5)Pouring system design is poor
Copper casting prevents bubbles from generating:
1)Correctly master the casting speed and avoid involvement gas
2)Organic impurities must not be mixed into the type (core) sand to reduce the gas loss of the molding material
3)Improve the exhaust capacity of (core) sand
4)Correctly use and handle cold iron
5)Improve casting system design