What is the difference between 201 stainless steel and 304 stainless steel?
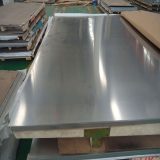
Aluminum alloys typically use alloying elements such as copper, zinc, manganese,, magnesium, with lighter and corrosion resistance compared to ordinary carbon steel, but corrosion resistance is not as simple as pure aluminum. In a clean and dry environment, the surface of the aluminum alloy will form a protective oxide layer.
Aluminum and aluminum alloys have lighter weight, better processability and corrosion resistance, is a good car lightweight material. The density of the aluminum alloy is only 2.68 g / cm3, only 30% of steel, under the conditions of the stiffness of the bend, the thickness ratio of aluminum to steel is 1.43, and the weight loss potential of aluminum is 49%, and the conditions such as bending strength Under the weight loss potential of aluminum on steel is 38%. Compared with other materials, aluminum alloys have the advantages of high strength and good corrosion resistance, making it widely used in civilian and industrial sectors, have become the preferred choice for metal materials such as electronics and transportation.
Today, key issues in social transportation are energy conservation and environmental protection, but the aluminum alloy is an effective way to achieve this goal. Therefore, since 1980, aluminum alloy materials have become the main materials in the transportation industry. At present, the use rate of aluminum alloy materials in the transportation industry has exceeded 25%, of which aluminum alloy materials have exceeded 15% in the automotive industry, which is gradually become the world's largest aluminum alloy material.
Aluminum alloys have good anti-impact, anti-vibration, anti-tensile and other mechanical properties, meet the standards of automotive and high-speed train materials. In addition, the compactness of the aluminum alloy material is only 33% of the steel material, thereby reducing the weight of the car itself, reducing driving resistance, saving fuel consumption.
In addition, the aluminum alloy itself has better wear resistance and corrosion resistance, no needle rust, greatly reduces maintenance cost and manufacturing cost. What '; in addition, aluminum alloy is more convenient for recycling compared to traditional steel. Generally, the recovery value of the scrapped car is; 6 times the height of a steel car. Therefore, aluminum alloy is widely used in motorcycles, trains, high-speed rail, subway and other vehicle structural parts and air conditioners, as well as skin and armored panels of different types of yachts and cruisers. In recent years, with the continuous development of my country's high-speed railway construction, the high-speed railway vehicle body uses a full aluminum alloy structure. In the field of automotive materials, the body skeleton often uses a 6xxx series high-intensity aluminum alloy.
In 1972, the US aluminum industry successfully developed a new type 7075 alloy; the use of titanium, manganese, etc. Currently, aluminum alloys have become the preferred materials for spacecraft and aircraft. In the civilian aircraft structure, the consumption of aluminum alloys is about 76%, such as the aluminum alloy consumption of Airbus A380 is about 71%.
At present, almost all types of aluminum alloy on the market can be put into the aerospace sector. Since the zinc copper alloy has high strength and good processability, it is commonly used in aircraft structural materials such as strategies and frames. Aluminum alloys are widely used in manufacturing rockets and aircraft low temperature tanks due to low density and low temperature toughness.
Alcoa, which is produced in the world, is 6% for electrical and electrical fields, while aluminum alloys are the main electron conductors. After all, first, the price of aluminum alloy is much lower than the copper alloy, which can strictly control the cost of cable laying. Second, since the density of the aluminum alloy is lower than the copper alloy, the aluminum alloy can obtain the required conductivity on the light and heavy basis, greatly reduces transportation costs. In addition, the recovery of the copper alloy is lower than the aluminum alloy, and has high corrosion resistance to reduce maintenance costs. At present, the high-voltage transmission line is generally used by aluminum bag steel core aluminum strand. This aluminum alloy has a high strength and good conductivity. There is also a big demand in the fields of household appliances, computers, especially the computer's disk substrate, packaging materials of household appliances, etc.
With the development of science and technology, I believe that in the near future, the aluminum alloy industry will grow rapidly and began to replace the status of steel, and its development trend is mainly reflected in the following aspects.
(1) Optimize the structure of capacity, focus on products with better performance such as corrosion resistance, finance, human materials to meet the needs of transportation, electronic packaging, aerospace and other fields.
(2) Develop aluminum matrix composite materials. Under the premise of the original alloy performance, many new aluminum-based composites have better physical and mechanical properties, which is also the main way for future development and research.
(3) With the development and popularization of aluminum alloy integrated technology, regeneration technology and recovery technology, the recovery rate is increasing.
(4) Innovation process equipment, improve production and processing methods, improve the quality of aluminum alloy, and speed up production.
The principle of aluminum die casting heat treatment is to control the heating rate in A; heating and accelerate cooling. Thus, the corrosion resistance of aluminum alloy is improved, and the processing capacity is improved, and the dimensional stability is obtained.
Characteristics of aluminum alloy heat treatment:
It is well known that high-carbon content can be highly hard, but its plastic is very low. However, after the aluminum alloy is quenched, the strength and hardness of the aluminum alloy will not increase immediately. As for plasticity, it is not reduced but increases. But this quenching alloy is placed for a period of time (such as 4-6 days), the strength and hardness increase, and the plasticity will decrease. The phenomenon of intensity and hardness after quenching of aluminum alloy is referred to as time efficacy. Aging can occur at room temperature, called nature aging. Or occurs within the temperature of the room temperature (e.g., 100 to 200 ° C), which is referred to as manual aging.
The aging hardening of aluminum alloy is a complex process. This not only depends on the ingredients and aging processes of the alloy, but also depends on the shortcomings of the alloy due to shrinkage during the production process, especially the number and distribution of space and dislocation. Current aging hardening is the result of solute atom segregation forming a hardening zone.
When the aluminum alloy is quenched and heated, a vacancy is formed. Since the speed is quickly cooled, these vacant is too late, can't be deleted; fixed; in crystal. The opening of these supersaturated solid solutions is bonded to solute atoms. The supersaturated solid solution is in an unstable state and transformed into a balanced state. It accelerates the diffusion speed of the solute atom, thus accelerating the separation of the solute atom.
The size and quantity of the hardening zone depends on the quenching temperature and the quench cooling speed. The higher the quenching temperature, the more the vacancy is, the more the number of hardening zones, the smaller the size. The larger the quenching cooling rate, the more space, which facilitates the increase of the number of hardened regions and reduces the size of the hardening zone.
One of the characteristics of the precipitated hardening alloy is that the balance solid solution increases with temperature, the solid solution increases with temperature. Most aluminum alloys meet this condition.
Aluminum alloy modification is to add a small amount of substances to the molten metal. It promotes the internal growth of the molten metal. During the production of aluminum alloy, metamorphism is an important process, and the addition of different metapulsics has different effects on the process of the alloy. Among them, each modifier has different functions, and common modifiers are:
Na can convert a short circular needle eutectary silicon to a good grain, reduce the eutectic temperature, increasing the coldness, and fine grains. Its refining effect is better, suitable for cold, slow sand and gypsum castings, and also has a function of dispersion castings (ingots), which acts in a highly airtight casting.
The amount of sodium salt modification method is low, and the preparation is relatively simple. Suitable for small batches, low requirements. Its disadvantage is that sodium is a chemically active element that will be oxidized during deterioration, strong combustion and release white smoke. It is harmful to the human body and the environment, and the operation is not safe, especially the crucible is easy to corrode and damage. Its deterioration is short, generally no more than 1 / h.
Sodium also increases the viscosity of aluminum magnesium alloys, weakening the casting performance. When the amount of sodium is large, it also catalyizes the grains of the alloy. Therefore, the magnesium-magnesium-magnesium alloy and aluminum silicon alloy in the magnesium content of the magnesium content generally do not modify the sodium salt modifier to avoid so-called "sodium criticization" phenomenon;
It is a long-term metamorphic method and is more applicable abroad. The amount of is 0.04-0.05% of the total weight of the drug. It has the advantage that its degradation is better than sodium salts, and its oxidation and combustion loss are less than sodium salts. In addition, the corrosion of the crucible is smaller than sodium salt, thereby extending the life of the crucible. This deterioration method is safer, more hygienic, and does not produce harmful to the human body and environment, and the deterioration effect is better than sodium salt, which is generally good safety; the deterioration is 80-90%.
The disadvantage is that the cost is higher than the sodium salt, and the intermediate alloy must be prepared in advance (otherwise the use of a ruthenium salt modifier), and there is no effect like sodium salt to disperse the casting dent.
This method is also a common long-term metamorphic method. If the amount of antimony is added is 0.2-0.3% of the total weight of the furnace, the long-term deterioration effect can be obtained, even if the aluminum alloy is merged, the deterioration effect is still effective. The metamorphic effect is related to the cooling speed of the alloy. Rapid cooling speed (such as casting in metal mold) has a good modification; the modification of slow cooling speed (such as gypsum mold or sand casting) is poor. If the sodium salt, strontium salt, the aluminum is added, and Sb cannot be added. This will form a Na3SB compound to make the alloy grains, and reduce the degradation of sodium and strontium.
To produce aluminum alloy die castings, modification is required. At present, there are many modifiers, and the manufacturer can choose the appropriate modifier according to the performance of the final product. Humans will never stop the pursuit of material performance. The results show that the deterioration process is complete, effective, and economical. The study of degradation processing will become a hot spot in the field of non-ferrous metals.
(1) Silica also called the shock of shocks using high speed sandstream to clean and roughen the metal surface. The surface treatment of this method can enable the surface of the workpiece to obtain a certain degree of cleanliness and different roughness, so that the mechanical properties of the surface of the workpiece are improved, thus increasing the fatigue of the workpiece, increasing it and the coating The adhesion, prolongs the durability of the coating film, and is also conducive to the leveling and decoration of the coating. This aluminum alloy process We often see more in all kinds of products of Apple, and more and more in the existing TV chassis cases or boxes.
(2) Polishing the use of mechanical, chemical or electrochemical methods, so that the surface roughness of the automobile aluminum piece is reduced to obtain a bright and flat surface processing method. Polishing processes are mainly divided into: mechanical polishing, chemical polishing, electrolysis polishing. Automotive aluminum parts can be mechanically polished + electrolytic polishing can be close to stainless steel mirror effect, giving people a high-grade simple, fashionable future (of course, if you want to leave fingerprints).
(3) Brushed metal brushes are a manufacturing process of scraping aluminum plates out of the line. Brushed wire can be divided into straight brushed, ripple brushed wire, ripple brushed, threaded drawings. Metal processing WeChat, the content is good, it is worthy of attention. The metal brushed process can clearly show each microfil mark, which makes the meticulous silk gloss in metal matte, and the products are more fashionable and technological.