What is the difference between 201 stainless steel and 304 stainless steel?
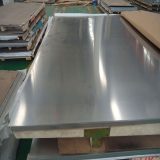
Tool steel is a steel with mechanical properties that make it an ideal material for tools. The hardness of the tool steel, its ability to maintain sharp edges or its resistance to wear and deformation are all noticeable. There are many alloys and carbon steels, usually made from heat treated and quenched products, suitable for use as tool steels. Tool steel comes in many different grades and is used to make tools such as stamping dies, construction equipment and shafts. In addition to making tools, it is also used in other applications where materials with the mechanical properties of tool steel are required.
The different grades of tool steel are generally classified according to a system created by the Society of Automotive Engineers (now SAE International) and the American Iron and Steel Institute called SAE Steel Grades or AISI/SAE Steel Grades. It classifies each type of steel with a letter indicating its properties or production method, such as the W-grade for water-hardening steels or the S-grade for impact-resistant steels. Each steel within these broad categories then receives an individual number following the letter.
The most common form of tool steel is grade W, which is a type of carbon steel due to its low cost. Some W-grade steels also include silicon, molybdenum or manganese to increase the toughness of the steel. It is called water hardening because water is used in the quenching process, a step in many steel production processes where the temperature of the heated steel is rapidly reduced. W-grade tool steel is hard, but brittle, and doesn't hold up well at temperatures above 302°F (150°C). W-grade tool steels are commonly used to make blades, such as shear blades and razors; machine parts for machines that do not experience high or high temperatures; and tools such as hammers, drills, and chisels.
Grades A, O and D are steels produced by cold working, during which the steel is subjected to mechanical stress until plastic deformation (permanent change in the microstructure of the steel). This process increases the tensile strength and hardness of the steel while reducing its ductility, and the final form of the steel is often used for purposes such as blades and machine tools. Grade O steel is oil hardened, while grade A steel is air hardened, which produces less deformation in the steel than water hardening. Grade D steel contains significant amounts of chromium, 10% to 18% of the alloy. In addition to chromium, grades A, O, and D steels are often alloyed with other metals, including manganese, tungsten, and vanadium, and non-metals, such as sulfur and phosphorus.
H-grade steels are hot-worked tool steels that result from plastic deformation of the steel caused by prolonged exposure to high temperatures. These steels have high strength and hardness, but slight deformation during cooling and thermal shrinkage make them less suitable for applications with tight engineering tolerances than cold-worked steels. Chromium, tungsten and molybdenum are common alloying elements in this grade of steel.
Grades T and M are types of high-speed steels that are characterized by their ability to maintain high hardness at high temperatures. This property makes it ideal for use in power cutting tools and stamping dies, where it can operate at higher speeds than other steels due to its resistance to heat generated by friction. T-grade steel is named for its high tungsten content, while M-grade steel contains a lot of molybdenum. Other alloying elements commonly found in these steels include vanadium, chromium and cobalt.
S-grade steels are tool steels known for their high impact resistance. They have a lower carbon content than other steel alloys, reducing their wear resistance but increasing their toughness. S-grade steel is used in equipment such as wind cannons that need to be able to withstand severe impacts.
Certain grades of tool steel have very specialized properties or uses. F-grade steel, like W-grade steel, is a water-hardening steel, but has excellent wear resistance. P-grade steel or plastic mold steel is used in injection molding and die casting machines. L grade or low alloy speciality steel is a very tough grade of steel with little alloying material and a high iron content.
The suitability of tool steel comes from the properties of its alloys:
(1) Unique hardness
(2) Wear resistance
(3) The ability to hold the cutting edge
(4) Red hardness
Other factors in tool steel selection include:
(1) Machining performance
(2) Grinding
(3) Tolerance
(4) Polishability