What is the difference between 201 stainless steel and 304 stainless steel?
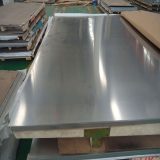
In industrial production, various devices will be used to produce production and processing, and many equipment operation is not allowed to open the copper parts, these accessories are used to improve the overall performance of the equipment. According to the purpose of the equipment, the performance and application of the accessory are also different. For example, it will have the following performance and use:
First, performance
1) The density of the copper casting is smaller than the cast iron and steel castings, but is higher than the intensity.
2) The copper alloy has a good surface gloss and good atmospheric, freshwater corrosion performance.
3) Pure copper has good corrosion resistance in oxidative acid such as nitric acid, acetic acid.
4) The casting has good thermal conductivity.
5) The casting has good casting performance.
6) Due to the large latent heat, the coagulation time of the copper fluid is much longer than the cast steel and cast iron under the same weight, and the fluidity is good.
Second, the application
1) Copper alloy castings can reduce structural weight under the same load, widely used in aviation, power machinery and transportation machinery manufacturing.
2) Widely used in the manufacture of civilian utensils.
3) Copper castings can be used in the chemical industry.
4) Parts for chemically produced heat transfer devices and internal combustion engine cylinder heads, piston, etc., are also suitable for copper alloy manufacturing.
5) The casting method such as metal type and pressure casting can be widely used in improving the intrinsic quality, dimensional accuracy, surface finish and production efficiency of castings due to its low melting point.
6) Used to cast thin-walled complex castings.
The copper casting parts have the advantages of high strength, high carrying capacity, good thermal conductivity, and has been widely used in the mechanical manufacturing industry. The production cost is low and aid for mechanical operation.
The peeling of copper castings, also known as peeling, layering, peeling, etc., is another cold-cooling form. Most of the outer surface or inner surface of the copper casting has a significant multi-layer metal skin, and most parts appear on a large plane. Arc around or sharp. In general, the castings will have significant peeling defects after shot or high temperatures. How to avoid this problem in production
1) The pressure of the copper fluid remains constant during die casting.
2) Partial mold temperature is suitable.
3) The surface of the copper casting and the skin are free, bubbles.
4) Avoid releasing the skin under external force.
5) Maintain sufficient dense or meshing on the surface of the copper casting.
6) Protect the dense layer.
Once the copper casting is peeled, it will not only affect its appearance, but also affect its quality. During the production of castings, manufacturers not only study how to choose a suitable die-casting process, but also integrate various factors to avoid peeling.
The treatment of the sand casting of the copper casting is multifaceted, first of all, it is necessary to handle the sand, the system's processing sand, in fact, in fact, two parts, one is for the treatment of old sand, The second is to handle some newly added sand, it can be said that these are many technologies. These should see if the actual operational capacity of the foundry can meet the requirements. Whether to see if the system of the shaped sand is A advanced level can be reached.
We know that in addition to the processing of the sand casting of the copper casting, we must pay attention to the use of suitable equipment, and pay attention to the coordination of each system, it can be said that these are A very critical influencing factor, daily should pay attention to the processing problems in this area when operating, and can better carry out sand casting of copper castings.
Only the cleaning work of copper castings can ensure that it produces a good effect, extending its service life and ensures its quality. The following is a detailed description of the cleaning method:
1) Surface cleanup: After the copper casting is shelled, the surface of the casting should be cleaned, especially the total residual oxide of the surface of the casting of the castings, the inner cavity, and blind holes, and cannot be cleaned.
2) Different welding: The part to be soldered is clean, so that the surface of the copper casting is completely cleaned, and the metal gloss is present. The defect size is low to large welding, and the rendering is large, the defect welding of the important part of the casting is annealed.
3) Cutting the gate and the rush: the main methods of cutting the gate and the rushing are: gas cutting, sawing machine, grinding wheel cut, hydraulic cutting, anode cutting, etc.
4) Casting cleans: The casting is related to the shape and size of the material and the production conditions after casting, and the shape and size of the material and the production conditions. If the cleaning work is advanced, the deformation and cracks of the copper casting are prone to. Big size, complex process castings should be longer, small size, and simple wall thickness thinning processes should be shorter.
5) Throwing blasting: When there is a special requirement for castings, it can be cleaned up. The shot blasting is the centrifugal force generated by the high-speed rotating shot blade wheel, and the iron pill is thrown to the surface of the casting to remove sand, viscame or oxidized skin remaining on the surface of the casting. In general, the surface of the casting after shot is related to the size of the iron pill.
By being cleaned by copper castings, it is possible to avoid the defects that are easily formed, ensuring the quality of the castings, preventing the problems of their functions due to these impurities.