What is the difference between 201 stainless steel and 304 stainless steel?
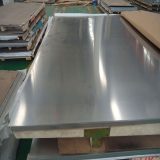
Bronze copper sleeve casting is a process in which copper alloy is melted into a liquid that meets certain requirements, and then poured into a mold. After cooling, solidification and cleaning, castings of desired shape, size and properties can be obtained. Since the casting blank is almost formed, only a small amount of machining or machining can be performed, reducing cost and manufacturing time to a certain extent. Casting is one of the basic processes of modern factory manufacturing. According to the characteristics and application development of cast bronze copper sleeves, casting methods can generally be divided into sand casting bronze copper sleeves and special casting copper sleeves.
1. Sand casting is the most commonly used method in production. It has the advantages of wide adaptability and simple preparation. However, the dimensional accuracy, surface quality and internal quality of castings produced by this method are far from meeting the requirements of mechanical parts, the production process is complex, mechanized and automated production is realized, and the investment is huge. When producing some special parts and castings with special technical requirements, the technical and economic indicators are relatively low. Therefore, the application of sand casting in foundry production is limited.
2. In addition to sand casting, various other casting methods different from sand casting have also been formed by changing the casting material, pouring method, liquid alloy filling form or solidification conditions of the casting. Foundry workers call other casting methods different from the sand casting process special casting. The methods of special cast bronze copper sleeves commonly used in machinery manufacturing are as follows:
(1) Investment casting. Castings with no or less cutting, high dimensional accuracy and low surface roughness are cast using investment molds and high-performance shells (molds).
(2) Metal mold casting. It is a method to use the metal mold to increase the cooling rate of the casting, realize multiple castings in one mold, and obtain a dense crystal structure of the casting.
(3) Die casting. By changing the filling and crystallization conditions of the liquid alloy, the liquid alloy is filled under high pressure and high speed, and it is formed and crystallized under high pressure to obtain precision castings.
(4) Lost foam casting. This is a method of gluing foam models that are similar in size and shape to the casting into a model family. After the refractory paint is painted and dried, it is buried in quartz sand for vibration modeling, and then pours liquid metal under certain conditions to vaporize the model, so that the liquid metal occupies the position of the model, and the required casting is formed after the liquid metal solidifies and cools.
(5) Centrifugal casting copper casing. It is a method of casting special castings such as rings, tubes, cylinders and sleeves by changing the filling conditions and solidification conditions of liquid alloys by centrifugal force.
(6) Continuous casting. It is an effective method for producing cast-rolled tubes and ingots under the conditions of continuous casting, solidification, and rapid-cooling mold cooling.
(7) Extrusion and liquid stamping casting. It is a comprehensive processing method of casting and forging.
Copper sleeves are used for high-load low-speed mechanisms. The principle of using copper sleeve is that the shaft must be hard, the copper must be soft, it must be filled with oil, tin bronze or brass.
The bronze copper sleeve is part of the mechanical equipment. Punch copper sleeves are mainly used in mining machinery and equipment, and are widely used. In the use of mechanical equipment, the copper sleeve is an indispensable part. The main materials of bronze copper sleeve are brass, bronze, aluminum bronze, phosphor bronze, lead bronze, etc., which are processed by sand casting and centrifugal casting. Like other copper products, copper sleeves also have their own characteristics.
1. The wear-resistant bronze copper sleeve has good wear resistance. Sleeves made of aluminum bronze copper sleeves of different materials have different properties. The internal structure of the centrifugally cast bronze copper sleeve is relatively compact, and there will be no looseness and porosity. Centrifugal cast copper casing has high hardness and durability.
2. Corrosion is another characteristic of copper casing. The copper sleeve mold has better corrosion performance and is mainly used in the atmosphere and fresh water. The copper bushing is not easy to be killed during use; the corrosion resistance of the copper bushing is mainly reflected in some chemical elements, so the corrosion resistance of the copper bushing is very good, and the fact that it will not bite is mainly due to its own properties, even without lubricants, can still work properly.
3. The compressive capacity of the bronze copper sleeve is very good, especially the surface pressure is very large, which can withstand the lateral pressure of the bearing. Under high load pressure conditions, the copper casing can still work.
These are the main characteristics of bronze copper sleeves, and its casting performance and cutting performance will also be very good, so bronze copper sleeves are an indispensable part of mining machinery and equipment.