What is the difference between 201 stainless steel and 304 stainless steel?
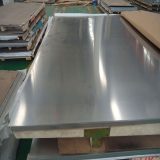
Only by doing a good job in the cleaning of copper castings can we ensure that they produce good results, prolong their service life and ensure their quality. Here is a detailed description of its cleaning method:
(1) Surface cleaning: After the copper casting is shelled, the surface of the casting should be cleaned, especially the total residual iron oxide scale on the surface of the casting with complex deep grooves, inner cavities and blind holes, which cannot be completely cleaned.
(2) Repair welding: Clean up the parts to be repaired, so that the surface of the copper casting is completely clean and shows a metallic luster. The defect size is welded from small to large, the repair welding area is large, and the defects in important parts of the casting are annealed after welding.
(3) Cutting gates and risers: The main methods of cutting gates and risers are: gas cutting, sawing machine, grinding wheel cutting, hydraulic cutting, anode cutting, etc.
(4) Casting cleaning: After casting, the cooling time in the mold is related to the shape and size of the material and production conditions. If the cleaning work is carried out in advance, it is easy to produce deformation and cracks of copper castings. The cooling time of castings with large size and complex process should be longer, and the cooling time of castings with small size and simple wall thickness reduction process should be shorter.
(5) Shot blasting cleaning: When there are special requirements for castings, shot blasting cleaning can be carried out. Shot blasting is to use the centrifugal force generated by the impeller of the high-speed rotating shot blasting machine to throw the iron shot to the surface of the casting to remove the residual sand, sticky sand or oxide scale on the surface of the casting. Generally speaking, the casting surface after shot peening is related to the size of the iron shot.
By regularly cleaning copper castings, it is possible to avoid easily formed defects, ensure the quality of the castings, and prevent the problem of inability to perform their functions due to these impurities.
Copper casting is the pouring of liquid metal into a cavity. After the liquid metal cools and solidifies, blanks or parts of various shapes can be obtained. These parts can be used in a variety of mechanical equipment. When it comes to solidification of castings, the way of solidification can be divided into three categories, which are explained below. In addition, we will cover the factors that affect the solidification of castings:
During the solidification process of copper castings, it is generally divided into three regions: solid region, solidification region and liquid region. The width of the solidification zone has a great influence on the solidification zone, and the solidification mode is divided accordingly.
(1) Intermediate solidification: The solidification of most alloys is carried out between layer-by-layer solidification and paste solidification.
(2) Layer-by-layer solidification: pure metals, eutectic alloys have no solidification zone during solidification. The liquid and solid phases in the cross section are clearly separated by a boundary. As the temperature decreases, the solid layer keeps increasing and the liquid layer decreases, reaching the center.
(3) Paste solidification: The crystallization temperature range of the alloy is very wide. During a certain solidification process, there is no solid layer on the surface of the copper casting, and the solidification zone runs through the entire section, first paste and then solidify.
According to the introduction of relevant experts, the factors affecting the solidification mode of castings are summarized as follows:
(1) Temperature gradient of copper castings. When the crystallization temperature range of the alloy is constant, the width of the solidification zone depends on the temperature gradient of the inner and outer layers of the casting. The smaller the temperature gradient, the wider the solidification zone. (The temperature difference between inside and outside is large, the cooling is fast, and the solidification zone is narrow).
(2) The crystallization temperature range of the alloy. Small range: The narrower the solidification zone, the more likely it is to solidify layer by layer. For example: sand casting, low carbon steel solidification layer by layer, high carbon steel paste solidification.
This paper summarizes several solidification methods of copper castings and the factors affecting the solidification of castings. Castings are prone to shrinkage porosity and other problems during the solidification shrinkage process. Therefore, it is necessary to control the solidification sequence, pay attention to the change of the wall thickness of the casting, and reinforce the thin-walled part of the thick-walled part to ensure the layer-by-layer solidification of the casting and the unobstructed feeding channel.