What is the difference between 201 stainless steel and 304 stainless steel?
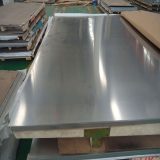
The oxidizing atmosphere (such as air, O2, CO2, H2O, etc.) during heating oxidizes the steel and forms FeO, Fe2O3, Fe3O4 and other oxides on the surface of the workpiece. At temperatures below 560 °C, relatively dense oxides such as Fe3O4 are mainly formed, which can isolate the steel surface from the oxidizing atmosphere and prevent further oxidation of the steel surface. However, the austenitization temperature of steel is mostly above 560 °C, and the steel is oxidized to form a loose oxide layer mainly composed of FeO. The thickness of the oxide layer increases with the increase of heating temperature and heating time, which not only leads to the burning loss of steel Increase the size, and make the size of the part smaller, the surface is rough, and more importantly, it seriously affects the quality of the subsequent heat treatment.
Decarburization during the heating process of steel, that is, the phenomenon that the carbon in the steel is burned and the carbon content on the steel surface is reduced. Decarburization often occurs along with oxidation, and the oxidizing atmosphere is also a decarburizing atmosphere. Although H2 is a reducing atmosphere, it is also a decarburizing atmosphere. Generally, the higher the carbon content in steel, the more serious the decarburization is. Due to decarburization, the carbon content on the surface of the steel decreases, resulting in a decrease in the mechanical strength of the steel, especially the fatigue strength of the workpiece and the wear resistance.
The overheating of steel means that the heating temperature is higher than the normal temperature, and the phenomenon is that the austenite grains of the steel are larger than normal, that is, the grains become coarser. As a result, the plasticity, toughness and strength of the steel are reduced, and the deformation of the workpiece after heat treatment increases, which may also lead to heat treatment cracks and scrap the workpiece. The overheated workpiece can generally be reheated at a lower temperature to re-fine the austenite grains and be remedied.
It refers to the phenomenon that the heating temperature is too high, and the austenite grain boundary or part of the grain boundary is oxidized or even melted. The consequence is that the workpiece to be processed is very brittle. If it is forged, it will crack, and the burnt workpiece can only be scrapped and cannot be saved, so it is fatal.
Heating the workpiece in vacuum is the most effective measure to prevent oxidative decarburization, and it is the development direction of heat treatment process. It is widely used in developed countries. The problem is that the equipment investment for vacuum heating is large and the process cost is high.
During the heating process of the workpiece, a certain protective atmosphere is filled into the furnace to ensure that the steel is heated in an atmosphere without decarburization, carbon increase and oxidation. Practice has proved that it is an effective and reliable method, and it is also a very common process in developed countries, and it is one of the development directions of modern heat treatment. However, a set of generating devices for producing a controllable atmosphere is required, and its application is limited due to the high cost and limited source of raw materials.
The workpiece is heated in a melted neutral salt solution, and the salt solution is fully deoxidized to ensure less or even no oxidation of the workpiece during the heating process. The main problem is that the salt that sticks to the workpiece is difficult to clean, and if the cleaning is not clean, it will lead to rust during storage and application. In addition, during the operation, the salt solution is easy to explode in contact with water, and it is easy to burn the human body if you are not careful, so you must pay great attention to safety.