What is the difference between 201 stainless steel and 304 stainless steel?
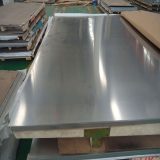
Heat the steel to a certain temperature, keep it for a certain period of time, and then slowly cool it to room temperature.
①Reduce the hardness of steel and improve the plasticity to facilitate cutting and cold deformation processing.
② Refine the grain, uniform the structure of the steel, improve the performance of the steel and prepare for the subsequent heat treatment.
③ Eliminate the internal stress in the steel. Prevent deformation and cracking of parts after machining.
Heat the steel to a critical temperature (the critical temperature of different steels is also different, generally 710-750°C, and the critical temperature of individual alloy steels can reach 800-900°C) above 30-50°C, keep for a certain period of time, and then slowly cool with the furnace (or Buried in sand to cool).
Refine grain, uniform structure, reduce hardness, fully eliminate internal stress and complete annealing is suitable for carbon content (mass fraction) in O. Forgings or steel castings below 8%.
Heat the steel to 20-30ºC above the critical temperature, and after heat preservation, slowly cool it to below 500°C and then release it for air cooling.
Reduce the hardness of steel, improve cutting performance, and prepare for subsequent quenching to reduce deformation and cracking after quenching, spheroidizing annealing is suitable for carbon content (mass fraction) greater than O. 8% carbon steel and alloy tool steel.
Heat the steel to 500-650ºC, keep it for a certain period of time, and then slowly cool it down (usually cooling with the furnace).
Eliminate the internal stress generated during welding and cold straightening of steel parts, and eliminate the internal stress generated during machining of precision parts to prevent deformation during subsequent processing and use. Stress relief annealing is suitable for various castings, forgings, welded parts and cold Extrusions, etc.
Heat the steel to 40-60ºC above the critical temperature, keep it for a certain period of time, and then cool it in the air.
①Improve organizational structure and machining performance.
② For parts with low requirements on mechanical properties, normalizing is often used as the final heat treatment.
③ Eliminate internal stress.
The steel is heated to quenching temperature, held for a period of time, and then rapidly cooled in water, brine or oil (individual materials in air).
① Make the steel parts obtain higher hardness and wear resistance.
② Make the steel parts get some special properties after tempering, such as higher strength, elasticity and toughness.
The steel is heated to the quenching temperature, and after being kept warm, it is cooled in a quenching agent.
Single-liquid quenching is only suitable for carbon steel and alloy steel parts with relatively simple shapes and low technical requirements. During quenching, for carbon steel parts with a diameter or thickness greater than 5-8mm, use brine or water cooling; for alloy steel parts, use oil cooling.
Heat the steel to the quenching temperature, after heat preservation, quickly cool it in water to 300-400ºC, and then transfer it to oil for cooling.
The flame of mixed combustion of acetylene and oxygen is sprayed onto the surface of the parts, so that the parts are rapidly heated to the quenching temperature, and then sprayed with water to the surface of the parts immediately. The flame surface quenching is suitable for single-piece or small batch production. Large medium carbon steel and medium carbon alloy steel parts subjected to shock loads, such as crankshafts, gears and guide rails, etc.
Put the steel part in the inductor, the inductor generates a magnetic field under the action of alternating current of a certain frequency, and the steel part generates an induced current under the action of the magnetic field, so that the surface of the steel part is rapidly heated (2-10min) to the quenching temperature. Spray water onto the surface of the steel.
The surface induction hardened parts are hard and wear-resistant, while the core maintains good strength and toughness.
Surface induction hardening is suitable for medium carbon steel and alloy steel parts with medium carbon content.
The quenched steel is heated below the critical temperature, kept for a period of time, and then cooled in air or oil.
Tempering is carried out immediately after quenching and is the last process of heat treatment.
① Obtain the required mechanical properties. Under normal circumstances, the strength and hardness of the parts after quenching are greatly improved, but the plasticity and toughness are significantly reduced, and the actual working conditions of the parts require good strength and toughness. After selecting the appropriate tempering temperature for tempering, the desired mechanical properties can be obtained.
②Stable tissue, stable size.
③ Eliminate internal stress.
The hardened steel parts are heated to 150-50ºC, kept at this temperature for a certain period of time, and then cooled in air. Low temperature tempering is mostly used for cutting tools, measuring tools, molds, rolling bearings and carburized parts, etc.
Eliminate the internal stress of steel parts due to quenching.
The quenched steel parts are heated to 350-450%, and cooled down after being kept for a period of time, generally used for various springs and hot stamping dies and other parts.
Make the steel parts have higher elasticity, certain toughness and hardness.
The quenched steel parts are heated to 500-650ºC, and then cooled after heat preservation. They are mainly used for important structural parts that require high strength and high toughness, such as main shafts, crankshafts, cams, gears and connecting rods, etc.
Make the steel parts obtain better comprehensive mechanical properties, that is, high strength, toughness and sufficient hardness, and eliminate the internal stress of the steel parts caused by quenching.
High-temperature (500-600ºC) tempering of quenched steel parts is mostly used for important structural parts, such as shafts, gears, connecting rods, etc. The quenching and tempering is generally carried out after rough machining.
Refine the grains, so that the steel can obtain high toughness and sufficient strength, so that it has good comprehensive mechanical properties.
Heat the quenched steel to 100-160°C, hold it for a long time, and then cool it down.
Eliminate internal stress, reduce part deformation, and stabilize dimensions, which is more important for parts with high precision requirements.
Place castings in the open air; steel parts (such as long shafts, leadscrews, etc.) are placed in seawater or suspended for a long time or lightly beaten. Parts to be naturally aged should be roughed first.
The steel parts are placed in a chemical medium containing some active atoms (such as carbon, nitrogen, chromium, etc.), and some atoms in the medium are infiltrated into the surface of the steel parts by heating, heat preservation, cooling, etc., so as to achieve change The chemical composition of the surface of the steel part makes the surface of the steel part have certain special properties.
Infiltrate carbon atoms into the surface of the steel.
Commonly used for wear-resistant and impacted parts, such as: wheels, gears, shafts, piston pins, etc.
The surface has high hardness (HRC60~65) and wear resistance, while the center still maintains high toughness.
Infiltrate nitrogen atoms into the surface of the steel.
Commonly used for important bolts, nuts, pins and other parts.
Improve the hardness, wear resistance and corrosion resistance of the steel surface.
Infiltrating carbon and nitrogen atoms into the surface of steel parts at the same time is suitable for low carbon steel, medium carbon steel or alloy steel parts, and can also be used for high speed steel tools.
Improve the hardness and wear resistance of the steel surface.
The metal parts are heated and oxidized in a very concentrated solution of alkali and oxidant, so that a layer of magnetic ferric oxide film is formed on the surface of the metal parts, which is often used in low carbon steel and low carbon alloy tool steel.
Due to the influence of materials and other factors, the film colors of the blackened layer are blue-black, black, red-brown, tan, etc., and its thickness is 0.6~O. 8µm.
Anti-rust, increase the appearance and luster of metal surface, eliminate stress during quenching.