What is the difference between 201 stainless steel and 304 stainless steel?
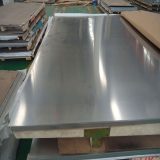
Commonly used die-castings have zinc, aluminum and magnesium; die-castings not only withstand high operating temperatures, but also fully recycle.
The die-casting mix is also:
①Excellent mechanical properties
②Good fluidity and filling
③Lightweight
④Generally has good corrosion resistance.
⑤Very good strength and hardness
⑥Accurate dimensional accuracy and stability.
⑦Fitting surface finishing
⑧Aluminum alloy castings have low density, low quality, high strength, good plastic, oxidation, corrosion resistance.
According to the requirements, it can be divided into two categories. A part of a part or relative movement velocity of a large load. Check items include dimensions, surface quality, chemical composition and mechanical properties (stretching, intensity, elongation, hardness); other components are other parts, inspection items include dimensions, surface quality, and chemical components.
These two categories involved aluminum alloy die casting products. For example, the first type is a die casting member that requires a larger load or higher relative speed. The second type of product is mainly electronic communication parts, chassis housing, radiator housing, and the like.
Heat treatment is an indispensable process for aluminum castings to achieve optimal mechanical properties. In addition, heat treatment has other functions:
①Each portion of the casting structure is uniform.
②Eliminate internal stress caused by solidification shrinkage.
③Stabilize the dimension and no longer change.
④Increase the workability of the material.
⑤Improve the corrosion resistance of the material.
The purpose of thermal treatment of aluminum castings is to produce a variety of available hardening elements such as copper, magnesium, zinc or polycoholic solids. A more uniform solid solution can be obtained by maintaining the aluminum casting at a high temperature of 535 ° C to 550 ° C.
The solid solution point of the aluminum casting is 530 degrees, the melting point is 555 degrees, and the aluminum casting will be melted into the aluminum water.
①When heating, the windmill cooling water should be successfully opened, and then the windmill work temperature is set to all open. Combustion Status: When the casting is inserted, the A is placed up, and the A is prohibited from being placed downward (the solution treatment).
②The temperature of the solution and aging treatment should be stable and uniform, which should be determined by the design strength, material, characteristics and test of the rim.
③The quenching water temperature is 60-80 degrees, so the aluminum casting is not easily deformed. The quenching time is calculated from the casting to start until the top casting is completely immersed in water. It is best to complete the instant quench in 16-20 seconds.
④The projects after solution treatment are fully inspected, including deformation inspection, molding, steel-based prevention, and quality abnormal tracking. After aging, the upper and lower layers of each car measures the hardness of the aluminum casting, which is 65-75 hb. With the continuous automatic operation, the casting is fed into the furnace after the preventer is the same. Operation in and away from the furnace according to the time set according to the timer.
Aluminum castings are widely used in automotive parts, mechanical manufacturing parts, computer accessories, telecom parts, pumps and valve parts. Aluminum alloy die castings are affected by various factors during the actual production process. Internal defects in the aluminum alloy die castings include air holes, shrinkage, loose holes, inclusions.
Characteristics and inspection methods: anatomical appearance check or inspection, the air hole has a smooth surface, and the shape is circular.
Approach:
①use dry and clean furnace, less impurities
②use vacuum die casting
③Guide metal hydraulic pressure balance, orderly filling cavity, which is conducive to gas discharge
④Exhaust groove parts to set reasonable and have enough exhaust power
⑤If there is a small coating, the spray is thin and uniform, and the coating is used.
Features and inspection methods: anatomical or flaw detection, the shape of the hole is irregular, not smooth, dark surface;
Macher and concentrate on a shrinkage, small hole and dispersed into a loose
Approach:
①Reduce pouring temperature and reduce shrinkage
②Improve the voltage ratio pressure, improve the density
③Modify the internal gate to make the pressure better, which is conducive to liquid metal replenishment
④Change the structure of the casting, eliminate metal accumulation parts, wall thickness as possible
⑤speed up the thickness of the cooling
Features and inspection methods: Mixed into the metal or non-metallic impurities in the die casting, see a point of irregularity, size, color, brightness different from the shape or a hole after processing.
Approach:
①Use a clean alloy, the stolen goods on the furnace need to clean clean
②Alloy solution must refine the gas, clean the slag clean
③cleaning cavity, pressing chamber
④Control the insulation temperature