What is the difference between 201 stainless steel and 304 stainless steel?
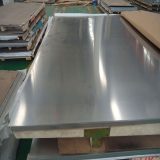
Titanium is an important structural metal developed in the 1950s. Titanium alloys are widely used in various fields due to their high specific strength, good corrosion resistance and high heat resistance. Many countries in the world have recognized the importance of titanium alloy materials, and have successively carried out research and development, and obtained practical applications. Titanium is the fourth B element in the periodic table. It looks like steel and has a melting point of 1 672C. It is a refractory metal. Titanium is abundant in the earth's crust, much higher than common metals such as Cu, Zn, Sn, and Pb. China is extremely rich in titanium resources. In the super-large vanadium-titanium magnetite discovered in Panzhihua area of Sichuan Province alone, the related titanium reserves reach about 420 million tons, which is close to the sum of the proven titanium reserves abroad. Titanium alloys can be divided into heat-resistant alloys, high-strength alloys, corrosion-resistant alloys (Ti-Mo, Ti-Pd alloys, etc.), low-temperature alloys and special functional alloys (Ti-Fe hydrogen storage materials and Ti-Ni memory alloys) .
Titanium alloys are alloys based on titanium with other elements added. Titanium has two homogeneous heterogeneous crystals: alpha titanium with a compact hexagonal structure below 882 °C and beta titanium with a body-centered cubic structure above 882 °C. According to the effect on the phase transition temperature, alloying elements can be divided into three categories: 1. Elements that stabilize the alpha phase and increase the phase transition temperature are alpha stabilizing elements, including aluminum, carbon, oxygen and nitrogen. Among them, aluminum is the main alloying element of titanium alloys. It has obvious effects on improving the strength at room temperature and high temperature, reducing the specific gravity and increasing the elastic modulus of the alloy. (2) β-stable phase and phase transition temperature drop are β-stable elements, which can be divided into two types: isomorphism and eutectoid. The former includes molybdenum, niobium and vanadium, while the latter includes chromium, manganese, copper, iron and silicon. (3) Neutral elements such as zirconium and tin have little effect on the phase transition temperature.
Oxygen, nitrogen, carbon and hydrogen are the main impurities in titanium alloys. Oxygen and nitrogen have high solubility in the alpha phase, which has a significant strengthening effect on titanium alloys, but reduces its plasticity. Oxygen and nitrogen contents in titanium are usually specified below 0.15-0.2% and 0.04-0.05%, respectively. The solubility of hydrogen in the alpha phase is very small. Excess hydrogen dissolved in titanium alloys can form hydrides, which can make the alloy brittle. Usually, the hydrogen content in titanium alloys is controlled below 0.015%. The dissolution of hydrogen in titanium is reversible.
Titanium is an isomer with a melting point of 1720°C and a dense hexagonal lattice structure at temperatures below 882°C, called alpha titanium; and a body-centered cubic lattice structure at temperatures above 882°C . called beta titanium. Titanium alloys with different microstructures can be obtained by gradually changing the phase transition temperature and phase content by adding appropriate alloying elements. Titanium alloys have three matrix structures at room temperature. Titanium alloys can also be divided into three categories: alpha alloys, (alpha + beta) alloys and beta alloys. China is represented by TA, TC and TB, respectively.
It is a single-phase alloy consisting of an alpha-phase solid solution. Both are α phase at normal temperature and higher practical application temperature. Compared with pure titanium, it has a stable structure, higher wear resistance and stronger oxidation resistance. Its strength and creep resistance are maintained at temperatures between 500 and 600 C, but cannot be enhanced by heat treatment, and the strength at room temperature is not high.
It is a single-phase alloy composed of β-phase solid solution. High strength without heat treatment. After quenching and aging treatment, the alloy is further strengthened, and its room temperature strength can reach 1372-1666 MPa. However, it has poor thermal stability and is not suitable for use at high temperatures.
It is a dual-phase alloy with good comprehensive properties, good structural stability, good toughness, plasticity and high temperature deformation properties. It can be processed under hot pressing and strengthened by quenching and aging. After heat treatment, compared with the annealed state, the strength is increased by 50%-100%, and the high temperature strength can work for a long time at a temperature of 400 500, and its thermal stability is not as good as alpha titanium alloy.
Among the three titanium alloys, the most commonly used are α-titanium alloys and α+β-titanium alloys. α-titanium alloy has the best machinability, followed by α+β-titanium alloy and β-titanium alloy. Alpha titanium alloy code TA, β titanium alloy code TB, α+β titanium alloy code TC.
Titanium alloys can be divided into heat-resistant alloys, high-strength alloys, corrosion-resistant alloys (Ti-Mo, Ti-Pd alloys, etc.), low-temperature alloys and special functional alloys (Ti-Fe hydrogen storage materials and Ti-Ni memory alloys) . The composition and properties of typical alloys are listed in the table.
Different phase compositions and structures can be obtained by adjusting the heat treatment process. It is generally believed that the thin equiaxed structure has better plasticity, thermal stability and fatigue strength; the needle-like structure has higher endurance strength, creep strength and fracture toughness; the equiaxed needle-like hybrid structure has better comprehensive properties.
Titanium alloys have high strength, low density, good mechanical properties, good toughness and corrosion resistance. In addition, titanium alloys have poor technical properties and are difficult to cut. Impurities such as hydrogen, oxygen, nitrogen and carbon are easily absorbed during thermal processing. The wear resistance is poor and the production process is complicated. Industrial production of titanium began in 1948. With the development of the aviation industry, the titanium industry is growing at an average rate of 8% per year. At present, the annual output of titanium alloy processing materials in the world has reached more than 40,000 tons, and there are nearly 30 types of titanium alloys. The most widely used titanium alloys are Ti-6Al-4V (TC4), Ti-5Al-2.5Sn (TA7) and industrially pure titanium (TA1, TA2 and TA3).
Titanium alloys are mainly used in the manufacture of compressor parts for aircraft engines, followed by rockets, missiles and high-speed aircraft. In the mid-1960s, titanium and its alloys were used in general industry to make electrodes in the electrolysis industry, condensers in power plants, heaters for oil refining and desalination, and environmental pollution control equipment. Titanium and its alloys have emerged as a corrosion-resistant structural material. In addition, it is used in the production of hydrogen storage materials and shape memory alloys.
Titanium alloy is a new important structural material used in the aerospace industry. Its specific gravity, strength and service temperature are between aluminum and steel, but it has high specific strength, excellent seawater corrosion resistance and ultra-low temperature performance. In 1950, the United States first used the F-84 fighter-bomber for non-load-bearing components such as rear fuselage heat shields, wind deflectors and tail covers. Since the 1960s, the use of titanium alloys has shifted from the rear fuselage to the mid-fuselage, partially replacing structural steel for the manufacture of important load-bearing components such as bulkheads, beams, flaps and slide rails. The use of titanium alloys in military aircraft has increased rapidly, reaching 20%-25% of the weight of the aircraft structure. Titanium alloys have been widely used in civil aircraft since the 1970s. For example, the use of titanium in Boeing 747 airliners exceeds 3,640 kilograms. Titanium for aircraft with Mach number less than 2.5 is mainly used to replace steel to reduce structural weight. For example, the American SR-71 high-altitude high-speed reconnaissance aircraft (flying at Mach 3 and flying at an altitude of 26,212 meters), titanium accounts for 93% of the weight of the aircraft structure, and is called an "all-titanium" aircraft.
When the thrust-to-weight ratio of the aero-engine increases from 4 to 6 to 8 to 10 and the outlet temperature of the compressor increases from 200 to 300 degrees Celsius to 500 to 600 degrees Celsius, the original low pressure compressor discs and blades made of aluminum must be replaced with titanium alloys , or use titanium alloys instead of stainless steel to make high-pressure compressor discs and blades to reduce structural weight. In the 1970s, the use of titanium alloys in aircraft engines usually accounted for 20%-30% of the total weight of the structure. It is mainly used to manufacture compressor parts, such as forged titanium fans, compressor discs and blades, cast titanium compressor casings, intermediate casings, bearing housings, etc. Spacecraft mainly use the high specific strength, corrosion resistance and low temperature resistance of titanium alloys to produce various pressure vessels, fuel tanks, fasteners, instrument belts, frames and rockets. Titanium alloy plate weldments are also used in artificial earth satellites, lunar modules, manned spacecraft and space shuttles.