What is the difference between 201 stainless steel and 304 stainless steel?
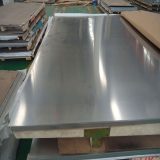
The key to welding stainless steel and nickel-based alloys is cleanliness and the selection of the correct welding consumables. This article is designed to help you step-by-step to successfully weld stainless steel and nickel-based alloys.
If the two base metals are of the same material, the base metal alloy material can be used as a guide for material selection. For example, when welding 316L and 316L metals, 316L consumables can be used. Past experience has shown that welds are prone to corrosion, which may require an increase in alloy content. As for how much alloy content needs to be increased, careful consideration must be given to avoid excessive alloy content and galvanic corrosion.
NOTE: Selecting the wrong consumables, or dilution too high, will result in a low alloy mixture that can lead to weld defects. The most common weld failure is cracking, however, weld embrittlement can also occur.
Therefore, the selection of the correct alloy welding material and welding process is critical to the successful completion of the welding job:
1)Do not use low alloy welding consumables when welding low alloys to stainless steel. Failure to do so will result in embrittlement of the weld.
2)When welding low alloys to stainless steel, do not use consumables below that grade. Embrittlement of the weld due to the formation of martensite.
3)Please use high alloy welding consumables specially designed for dissimilar metal welding, such as 309, 312, etc.
When welding dissimilar stainless steel or dissimilar nickel, see the Dissimilar Metal Welding Guidelines. In general, the best approach is to use consumables designed for the higher alloyed metal of the two. For example, when welding 304L and 316L base metals, use 316L filler metal.
1) When welding stainless steel to nickel-based alloys, do not use stainless steel welding consumables, as it is likely to cause centerline cracks. This is due to the dilution that occurs on the nickel metal side of the weld. If the nickel content of the stainless steel deposit is too high, it will lead to an imbalance of composition, which makes it more prone to cracks.
When choosing welding parameters, heat input should be as low as possible to minimize distortion. When the thermal deformation is too high, the base metal will be overstretched and stress cracks will occur.
Heat input = (current*voltage*60)/welding speed. The lower the current or voltage, the lower the heat input. The faster the welding speed, the lower the heat input. For example, direct welding is faster and has lower heat input than weaving.
Adjust current or voltage to optimize:
1)Arc Stability
2)Penetration (the lower the voltage, the shallower the penetration)
3)Weld spatter (reduce wire feed speed, or increase voltage)
4)Undercut (The higher the current, the easier it is to cause undercut. The welding speed can also be reduced so that the weld pool fills the bottom edge)
5)Dilution (the shallower the penetration, the lower the dilution)
Use a short-circuit welding process to minimize burnout of alloying elements.
Remove or avoid all possible sources of contamination, including corrosion from: dirt, oil, grease, scale, paint, and marking inks that may contain chlorides.
If splash-proof media are used, special materials for stainless steel must be used. If compressed air is used to cool or dry welds, attention must be paid to the oil they contain.
Be aware that the process of degreasing can create contaminants that can adversely affect soldering and produce dangerous toxic fumes.
Do not mix stainless steel and carbon steel products to avoid iron contamination. Iron particles can trigger localized corrosion.
Avoid condensation. Warm up welding workpieces stored outdoors to room temperature to avoid condensation. Monitor the humidity of the shielding gas.
For welds prepared by plasma cutting, or cutting processes using nitrogen or plasma gas, fine grinding is required to clean the metal, as weld nitriding can cause rust in the heat-affected zone of the finished weld.
Use stainless steel specific, uncontaminated sanding tools.
Compared with carbon steel, the thermal expansion rate of stainless steel is 50% higher. Nickel-based alloys have a slightly lower expansion rate. Spot welding or jump welding is frequently used to reduce stress. Minimize the use of the weaving technique as it reduces movement speed and increases heat input. On stainless steel or nickel-based alloys, the direct welding operation is preferred when welding.
Avoid using narrow gaps. The root of the weld must be at least equal to the diameter of the welding material. This is especially important when welding materials with low weld flow properties, such as duplex stainless steels and nickel-based alloys, to avoid underpenetration or undercuts at the root.
This step is very important. The purpose of post-weld cleaning is to ensure the proper formation of a chromium oxide film on the surface for optimum corrosion resistance: the smoother the surface, the better the corrosion resistance. The heat from welding can burn away the chromium on the surface, which can lead to corrosion. In order to avoid rust, it is very important to remove chromium-poor areas after welding by chemical or mechanical cleaning.
Stainless steel brushes and other tools are highly recommended to prevent iron particles from adhering to the surface and causing rust.