What is the difference between 201 stainless steel and 304 stainless steel?
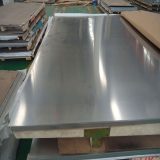
Divided by chemical composition::
(1) Carbon steel: S50C, S55C
(2) alloy steel: Ⅰ low alloy steel (≤5%); Ⅱ alloy steel (5%to 10%); Ⅲ high alloy steel (> 10%).
Divided into: plastic mold steel, cold mold steel, heat -making mold steel.
Generally, plastic mold steel is supplied in a pre -hard state (that is, pre -quality = quenching+high temperature recovery).
As the use of plastic molds, there are various conditions, and the steel for mold should meet the following requirements:
(1) Good mechanical processing performance: The geometric shape of the plastic mold cavity is very complicated, often with deep holes, deep grooves, narrow seams and other processing parts. Steel must have easy cutting performance.
(2) Good polishing performance: No matter what kind of plastic molds, the allowable surface roughness of its cavity is extremely small, and almost all requires mirror gloss. To achieve mirror gloss, the main point is that steel must have the hardness of not less than 38HRC, preferably 40-46HRC, and 55HRC is the best. To achieve a mirror gloss, first of all, the miscellaneous objects in the steel should be as small as possible, and there must be no bubbles, and the fiber tissue is uniform. In order to reduce wear in large quantities, in addition to the surface hardness of the cavity, the surface roughness is also an important condition.
(3) There are good surface corrosion processing: There are many molds that require forming of molds to form the patterns of various other substances. Such as leather patterns, silk patterns, cloth patterns, fine patterns, etc. This requires the texture of the steel to be fine and uniform, otherwise the surface corrosion effect is not good.
(4) It is both abrasion resistant and tough: plastic molds have a long -term heat transfer load, and they have suffered friction for a long time. If you only consider the side of friction without considering the load of the heating intercourse, if it is made of high -carbon and high alloy steel used in cold molds, it will inevitably cause lack of toughness and cracking.
(5) Good quenching performance and small deformation: Most of the cavities of plastic molds, especially thermosetry plastic molds, must be performed. This requires the steel to have better quenchtability and small deformation. Generally, the thermoplastic plastic forming mold is used, and it can be treated with quality adjustment and pre -cirrhosis. The molding of thermosetry plastic must be hardened.
(6) Good electricity processing: The concave cavity of plastic molds is often machined, and the surface of the surface after discharge processing should be shallow to facilitate polishing. Polishing is the most time -consuming in plastic cavity processing. Time increases costs. At present, the technology of automatic polishing has not yet reached the practical stage, and it is still dominated by hand -polishing. The thickness of the hardening layer increases.
(7) There is corrosion resistance: Some plastic, such as polyvinyl chloride can produce gases hydrochloride during forming, which is corrosive. Therefore, for plastic molds for corrosive gases, the corrosion resistance of steel must be considered.
(8) Weldability: In the processing of cavity, it is inevitable to replenish welding. Therefore, mold steel must have a good welding performance.
When choosing plastic mold steel, consider it one by one according to the following conditions, and finally make a decision.
(1) The production batch of plastic parts: molds are high -efficiency production tools. The service life of each mold is directly related to the cost of the component. When designing molds, in addition to considering the number of cavities of each mold according to the output, its service life must be considered. If the batch is small, the requirements for steel can be lower; when the batch is large, high -quality steel must be selected to ensure the service life and try to avoid repeated molds.
(2) Dimensions of plastic parts: The size and accuracy of plastic parts depends to a large extent on the manufacturing accuracy of the mold, and it determines the qualification rate of the device. For plastic parts that require high precision (3, 4 precision of SJ/T10628-95) and super high precision (1, 2 precision of SJ/T50628-95), high -quality mold steel should be selected.
(3) The complexity of the parts: the more complicated the parts, the more difficult it is to process the cavity. Therefore, steel with good cutting performance must be selected. The complication of the parts is high, the size is large, and the processing parts are large. Therefore, the stress deformation of processing must be considered.
(4) The volume of the parts: the larger the parts, the greater the cutting volume of the cavity. When cutting with a large amount of knife, the cutting stress is also large. Therefore, it is best to use easy cutting steel for the molds of large pieces. The part of the parts, the volume of the cavity is small, the tool (mainly milling cutter) used is low and the cutting amount is small. When selecting steel, you should choose a uniform texture, and the alloy carbides are distributed fine and well -proportioned. Small molds are mostly planned first, then processing, and the possibility of processing must be considered.
(5) The appearance requirements of the parts: If the plastic part is a decorative part, the quality of the surface can greatly affect the sales of the product. For plastic parts with high requirements for plastic parts, it is best to choose vacuum melting or electric slag melting steel to achieve the best cavity polishing effect.
The production of transparent plastic products, especially optical instruments, has high requirements for the polishing of molding molds (ie, mirror processing).
Factors affecting mirror processing performance are:
(1) Steel Metallurgical Quality: Easy -to -cut steel must be used. The use of VAD, VAR, ESR and other processes can improve the purity of steel, thereby improving polishing performance.
(2) Organizational unevenness: the effect of micro -analysis. The measure is to master the crystal quality of the steel and the crystal quality of the steel ingots; fully forged to ensure density; it is heated or ESR.
(3) Hardness: High hardness is good for mirror polishing. The surface carburizing or decarburization after thermal treatment causes the surface quality to deteriorate and affects polishing performance.
(4) Polishing technology: Avoid excessive surface contact stress during polishing. Otherwise, the softering substrate will be eroded, leaving carbides out, leaving defects on the surface of the steel.
(1) It is conventional that there are Bushi (HB), Luoz (HRC), Vita (HV), and Lish (HL) hardness, etc. Among them, HB and HRC are more commonly used.
(2) The range of HB has a wide range of applications, commonly used in supply, and CU and Al are also available. HRC is suitable for characterizing high hardness materials, such as heat treatment hardness. The difference between the two is that the test head of the hardness meter is different.
(3) Under certain conditions, HB and HRC can be swapped. Its conversion formula can be recorded as: 1hrc≈1/10HB.
(4) HV-suitable for micro-analysis, CU and Al are also available.
(5) HL-Practical hardness meter, convenient measurement, but requirements for the thickness of the sample.