What is the difference between 201 stainless steel and 304 stainless steel?
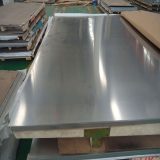
Decarburization is a phenomenon that occurs when the oxidation rate of the steel surface is smaller than the diffusion rate of carbon. Both oxidation and carbon diffusion occur strongly at high temperatures above the A1 transformation point. The decarburization can be controlled by the heating atmosphere in the furnace, and the oxidizing atmosphere can cause decarburization or oxidation. Especially when there is water vapor in the furnace, decarburization is very serious.
Also, in the heat treatment of rough forgings, when the oxide scale is knocked off by shot peening in advance. If the shot peening is too much, there will be more oxidative decarburization, which should be paid attention to.
During heat treatment such as heat, iron and steel combine with oxygen in the air to form iron oxide, a phenomenon called oxidation. The film formed due to oxidation is oxide skin. Scale can prevent rapid cooling during quenching, causing so-called quenching soft spots. Generally, when the oxidation rate of oxygen is larger than the expansion rate of carbon, oxide scale is generated; otherwise, decarburization occurs.
Therefore, a thick oxide scale can be generated without decarburization in the strongly oxidizing furnace gas whose oxidation rate is significantly larger than the diffusion rate. Therefore, it has become common knowledge that high carbon steel (SK) should be annealed in a strong oxidizing atmosphere.
Generally, the scale of high carbon steel is dense, and the scale of low carbon steel is loose and easy to peel off. Fe2O3, the lower layer is Fe3O4, the innermost layer is Fe: and above the As transformation point, the order of the oxide scale from the outer to the inner layer is: Fe2O3, Fe3O4, FeO.
Crocodile-like oil marks; oil attached to the steel surface is not completely burned when heated, and the pattern formed on the surface remains. Because it looks like crocodile skin, it is called crocodile-like oil marks. When heating in a heavy oil furnace, crocodile-like oil marks are prone to occur when heavy oil drops on the surface of the quenched part, so we must pay attention.
Sweating is a phenomenon in which a composition with a low melting point shows small grains on the steel surface when heated or cooled. It is called sweating because it is like a person sweating. For example, high-speed steel, if heated to a temperature close to melting (1320℃~1350C) and quenched, the surface will sweat. According to the size and number of the sweat particles, it can be known whether it is heated and quenched at an appropriate temperature.
Wrinkled suriace is a phenomenon in which the melting temperature of steel decreases due to carburization during heating, thereby causing wrinkles on the surface. It is a surface melting phenomenon that often occurs in high-speed steel during quenching and heating.
The warls are when the steel is heated in a salt bath furnace, in order to prevent decarburization, charcoal powder is sprinkled on the surface of the salt bath. This charcoal sticks to the surface of the part and melts, often producing small wart-like particles. It is usually called a wart. In conclusion, warts are evidence of carburization.
After the steel is heat treated, due to the expansion of the gas (mainly hydrogen) under the surface, bubbling occurs on the surface, which is also called blister ● This phenomenon often occurs when pickling parts are heated.