What is the difference between 201 stainless steel and 304 stainless steel?
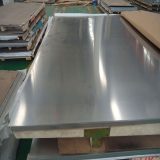
1) Stable and controllable heating system. The heating system of the blank is medium frequency induction heating, infrared thermometer and three-channel temperature sorting system, which can conveniently control the heating temperature and sort the blanks with unqualified heating temperature.
2)determine the appropriate quenching temperature, and can be effectively controlled. The suitable forging waste heat quenching temperature should be determined according to the test. In actual operation, it can be realized by controlling the forging heating temperature and the residence time after forging. The residence time after forging is recommended to be no more than 60s for carbon steel and 20 to 60s for alloy steel.
Configure infrared thermometer and temperature sorting system to sort out the forgings below the quenching temperature; when the forging heating temperature is stable and the forging process is also stable, the process time measurement and alarm system can be configured, and the quenching temperature can be controlled by controlling the process time. the goal of.
3) good quenching system. On the premise of ensuring the quenching effect, select a quenching agent with a slower cooling capacity to prevent serious quenching deformation and cracking. Because the quenching temperature of forging waste heat is higher than that of ordinary quenching, the hardenability of forgings is good, so oil or PAG quenching agent is generally used for carbon steel and alloy steel.
The quenching tank should have sufficient volume, and the cooling time should be controllable. In addition, the quenching medium circulation, cooling system and heating device should be configured, the temperature of the quenching medium should be automatically controlled, and an air extraction device should be configured. Strengthen the maintenance of the quenching medium, regularly check the cooling performance of the quenching medium, clean the impurities such as oxide scale in the liquid tank and the circulation system, and keep the quenching medium clean.
4)Arrangement of tempering and tempering furnace after quenching. After quenching, there is a large stress inside the forging, which leads to large deformation or even cracking during the placement process. In order to prevent deformation and cracking of parts after quenching, forgings should be tempered in time after quenching. The time that can be put aside after quenching is related to the material, shape and ambient temperature of the forging, and should be determined according to the test. In order to save energy, improve the utilization rate of the tempering furnace, and reduce the energy consumption of heat preservation, the forgings quenched by waste heat are generally tempered in the heat treatment workshop.
1) Appropriately control the temperature of the forgings before entering the furnace. When the temperature of the parts is high, the forgings need to be cooled by blowing air to reduce the temperature of the parts to the required normalizing temperature. At the same time, the power of the heat treatment furnace needs to have a certain margin, and heating is performed before starting production and when the temperature of a small number of forgings is low.
2) Determine a reasonable holding time. If the holding time is too long, the grains will be coarse, and if the holding time is too short, the microstructure transformation will be insufficient. It can be determined by testing according to the material, shape and size of the forging.
1) Temperature control of forgings after forging. The temperature of the forgings after forming must be above Ar3 (for hypoeutectoid steel), and the direct quenching method can be used when the temperature of the forged parts is stable; when the temperature of the forged parts fluctuates greatly or the cross-section of the forgings changes greatly, the temperature uniformity process must be increased. Make the temperature of the parts uniform before quenching, otherwise, the temperature of the forgings or different sections after quenching will vary greatly, resulting in abnormal structure (bainite or martensite).
2) Quench cooling speed control. The rapid cooling of the forgings is required in the quenching process, and the temperature of the same forging and the same batch of forgings after cooling is uniform (or similar). At the same time, it is necessary to control the quenching speed, and the excessively fast quenching speed will produce Widmandelweiss structure in the forging structure. Generally, the quenching speed is controlled at 30-42°C/min.
3) Temperature control after quenching. After quenching, it must be ensured that the temperature of the forging is in the pearlite transformation zone and cannot be lower than the bainite transformation start temperature (Bs), otherwise bainite (or granular bainite) structure will appear in the structure; if the temperature is too high after quenching, it will lead to The amount of proeutectoid ferrite increases, and the pearlite lamella spacing is large after the microstructure transformation, resulting in low hardness of the parts. The temperature of the forgings after quenching is generally controlled at 80-100°C above the Bs temperature of the material.
4) The choice of isothermal temperature. The level of isothermal temperature directly affects the hardness of the forgings after isothermal normalization. The higher the isothermal temperature, the lower the hardness, and the lower the isothermal temperature, the higher the hardness. The isothermal temperature is generally 50 to 80°C above the Bs temperature of the forging material, and the specific temperature should be determined by testing according to the material and shape of the forging.
5) Determination of isothermal holding time. Pearlite transformation occurs in the isothermal process, so there must be enough holding time. For example, if the isothermal time is too short, the supercooled austenite will not be completely transformed into pearlite, and will be transformed into bainite or martensite in the subsequent cooling process. body, resulting in unqualified tissue and high hardness after isothermal treatment. The isothermal time can be preliminarily determined according to the isothermal transformation curve of the material, and adjusted according to the test situation.