What is the difference between 201 stainless steel and 304 stainless steel?
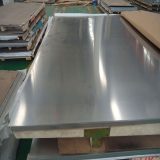
Low carbon steel, also known as mild steel, carbon content from 0.10% to 0.30% low carbon steel is easy to accept various processing such as forging, welding and cutting, commonly used in the manufacture of chains, rivets, bolts, shafts, etc.
Carbon steel with a carbon content of less than 0.25% is also called mild steel because of its low strength, low hardness and softness. It includes most ordinary carbon structural steel and some high-quality carbon structural steel, most of which are used for engineering structural parts without heat treatment, and some are used for mechanical parts that require wear resistance after carbonization and other heat treatment.
The annealed structure of low carbon steel is ferrite and a small amount of pearlite, its strength and hardness are low, and its plasticity and toughness are good. Therefore, its cold formability is good, and cold forming can be carried out by methods such as hemming, bending and stamping. This steel fin has good weldability. Low carbon steel with very low carbon content has low hardness and poor machinability, and quenching treatment can improve its machinability.
Low carbon steel is generally rolled into angle steel, channel steel, I-beam, steel pipe, steel strip (steel plate), and is used to make various building components, containers, boxes, furnace bodies and agricultural machinery. High-quality low-carbon steel is rolled into sheets to make deep-drawn products such as car cabs and generator covers; it is also rolled into bars to make mechanical parts with different strength requirements. Low carbon steel is generally not subjected to heat treatment before use, and carbon content of more than 0.15% is carburized or cyanided, which is used for shafts, bushings, sprockets and other parts that require high surface layers and good wear resistance.
Mild steel has limited use due to its lower strength. Appropriately increasing the manganese content in carbon steel and adding trace amounts of vanadium, titanium, niobium and other alloying elements can greatly improve the strength of the steel. If the carbon content in the steel is reduced and a small amount of aluminum, boron and carbide forming elements are added, the ultra-low carbon bainite group can be obtained with high strength and good ductility and toughness.
Medium carbon steel is carbon steel with a carbon content of 0.25% to 0.60%. There are killed steel, semi-killed steel, boiling steel and other products. In addition to carbon, it can also contain a small amount of manganese (0.70% to 1.20%). According to product quality, it is divided into ordinary carbon structural steel and high-quality carbon structural steel. Good thermal processing and cutting performance, poor welding performance. The strength and hardness are higher than those of low carbon steel, while the plasticity and toughness are lower than those of low carbon steel. Hot-rolled and cold-drawn materials can be used directly without heat treatment, or they can be used after heat treatment. The quenched and tempered medium carbon steel has good comprehensive mechanical properties. The highest hardness that can be achieved is about HRC55 (HB538), and σb is 600-1100MPa. Therefore, among various uses of medium strength level, medium carbon steel is the most widely used, in addition to being used as a building material, it is also widely used in the manufacture of various mechanical parts.
Medium carbon steel has higher carbon content than low carbon steel, higher strength and poor weldability. Commonly used are 35, 45, 55 steel. The main characteristics of medium carbon steel electrode arc welding and its casting welding repair are as follows:
(1) The heat affected zone is prone to hardened structure. The higher the carbon content and the greater the thickness of the plate, the greater this tendency. If the welding materials and process specifications are improperly selected, cold cracks are likely to occur.
(2) Due to the high carbon content of the base metal, the carbon content of the weld is also high, which is prone to hot cracks.
(3) The sensitivity to pores increases due to the increase of carbon content. Therefore, the requirements for deoxidation of welding materials, degreasing and rust removal of base metals, and drying of welding materials are more stringent.
High carbon steel, often called tool steel, contains from 0.60% to 1.70% carbon and can be hardened and tempered. Hammers, crowbars, etc. are made of steel with a carbon content of 0.75%; cutting tools such as drills, taps, reamers, etc. are made of steel with a carbon content of 0.90% to 1.00%. Welding of high carbon steel.High carbon steel has poor weldability due to its high carbon content. Its welding has the following characteristics:
(1) The thermal conductivity is poor, and there is a significant temperature difference between the welded area and the unheated part. When the molten pool is rapidly cooled, the internal stress caused in the weld is easy to form cracks.
(2) It is more sensitive to quenching, and martensitic structure is easily formed in the near seam area. Due to the effect of tissue stress, cold cracks occur in the near seam area.
(3) Due to the influence of welding high temperature, the grains grow rapidly, and carbides are easy to accumulate and grow on the grain boundaries, making the welds fragile and the strength of the welded joints reduced.
(4) Hot cracks are more likely to occur when high carbon steel is welded than medium carbon steel.