What is the difference between 201 stainless steel and 304 stainless steel?
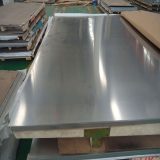
Standard 300 series deposited metals contain a certain amount of ferrite, which will help reduce microcracking. Microcracks can grow into continuous cracks, which usually appear in the center of the weld. Microcracks are usually caused by the formation of low melting point intermetallic compounds at the grain boundaries of solidified welds and the high thermal expansion rate. Ferrite increases the area of grain boundaries and, therefore, dissolves and reduces the amount of low-melting intermetallic compounds.
Since nickel and super austenitic alloys do not contain ferrite, they are more likely to crack. To reduce the risk of cracking, the following must be observed:
Due to the higher nickel content, the molten pool flows more slowly. In order to avoid incomplete root penetration, it is recommended to use a wider groove and a larger root gap compared to general stainless steel.
The lower the heat input, the lower the likelihood of cracking. It is best to use small diameter welding consumables with lower welding currents. In general, a maximum heat input of no more than 25 kJ/inch (1 kJ/mm) is appropriate.
Concave weld profiles should be avoided. It is best to produce flat or slightly raised welds.
When welding ferrite-free alloys, it is better to use lower interpass temperatures to reduce thermal stress. The maximum recommended interpass temperature is 300°F (150°C).
Duplex steels are very different from standard stainless steels. Its ferrite and austenite contents are about 50%, respectively. If not welded properly, the dual-phase steel series materials will produce brittle phases or precipitates, which can easily lead to pitting corrosion. If this is clearly recognized and the recommended welding procedures are followed, it is easy to achieve a weld with good mechanical properties and good corrosion resistance.
Exaton can provide welding guidelines to help you successfully weld duplex base metals together.
In general, the following parameters are required:
Due to the properties of ferritic materials, the flow of the molten pool will be poor. In order to avoid incomplete root penetration, it is recommended to use a wider groove and a larger root gap compared to general stainless steel.
Due to the properties of ferritic materials, the flow of the molten pool will be poor. This can be compensated for by the selection of an appropriate shielding gas, and it is beneficial to achieve a balance of austenite and ferrite. The choice of backside shielding gas can also improve corrosion resistance.
In order to achieve the optimum ferrite to austenite ratio, the heat input must be properly controlled. The recommended heat input range depends on the type of duplex stainless steel being processed.
To prevent the formation of brittle phases, dual-phase steel welding requires specific interpass temperatures. The appropriate interpass temperature depends on the weld grade and base metal thickness.
Due to the poor flow properties, the welding speed of the ferritic stainless steel alloy itself is relatively slow.
In many industrial applications, vessels must meet the relatively high pressure requirements of various pressure vessel codes such as ASME. At the same time, in order to prolong the life of the container, anti-corrosion treatment is required.
A common solution is to use low-alloy high-strength steel to make the vessel, and to use different welding processes to deposit the vessel with various high-alloy materials. Commonly used welding processes are gas shielded welding, argon arc welding, manual arc welding and submerged arc welding using wire or wire/flux combinations. Over the past few decades, the use of welding strips has become increasingly common, whether using submerged arc welding or electroslag welding.
In general, to achieve a tightly bonded deposition layer, superalloy welding consumables must be used in the first layer. Subsequent layer surfacing operations are performed using consumables with the desired chemical composition for the final deposited layer.